N2NP Series
N2 Generators (95.000% to 99.999% Purity)
The N2NP series of PSA nitrogen generators are designed to produce a wide range of flow rates at nitrogen purities of 95% up to 99.999%. Next, offers a standard twin tower (PSA) and a sequential twin tower (PSA) nitrogen generator.
Next N2NP Nitrogen differs from competition as the N2NP Series is a completely automatic system. The generator does not require system setup due to its ability to automatically sample nitrogen purity and switches to outlet when N2 purity is set.
PSA generators separate nitrogen from compressed air utilizing Pressure Swing Adsorption (PSA) technologies. Compressed air, which consists of approximately 21% oxygen and 78% nitrogen, is passed through a bed of Carbon Molecular Sieve (CMS). The CMS media preferentially adsorbs O2 and moisture, allowing the N2 to pass through as a product gas at the specified pressure. While one of the towers is in the adsorption phase, the other tower is being regenerated, by de-pressurizing and allowing the CMS to release the adsorbed gases to the atmosphere. The cycle then repeats, allowing for constant flow of a controlled Nitrogen purity and flow. What sets the N2NP series Nitrogen generators apart from competitors is its automatic purity vent outlet valve, where competitors use a manual. The product range is designed for medium to large flow rates and engineered to stand up to any harsh environment it faces.
Next nitrogen generators eliminate the need for traditional nitrogen shipments and storage, providing you with real cost savings.
Green energy
The nitrogen product dew point is about -58°F/-50°C, at atmospheric conditions. The PSA system uses no process water or chemicals for gas purification and generates no wastewater in the exhaust stream. It operates at ambient temperatures of 40 to 104°F/5 to 40°C, and the design pressure is 150 psig/10 bar.
Adjustable Flow and purity — from 95% to 99.999%
— from 95% to 99.999% Next offers 22 standard N2NP PSA units. Sizes are a function of the required product flow rate, purity, temperature and pressure. All are suitable for use on-site and equipped with all the components necessary to concentrate nitrogen from air.
N2P Series Features
- Mounted Filtration
- N2GC-2300, 7” HMI -Touch Screen Controller
- UL, CUL, Electrical Certifications
- ASME, CRN Code Welded Pressure Vessel Certification
- Stainless Steel Angle Body Valves / Butterfly Valves
- Tower Pressure Relief Valves
- Nitrogen sample pressure gauge & Regulator
- Liquid Filled Tower Pressure Gauges
- Nema-4 Electrical enclosure
- Separate Drain and Fill port
- Fail-Safe Design
- Oxygen Analyzer / Nitrogen Purity Sensor
- Equalization Adjustment Valve
- Flow Adjustment Valve
- Flow N2 out Adjustment Valve
- Flow N2 Sample Adjustment Valve
- Repress Adjustment Valve
- Flow Pressure Regulator
- Inlet Pressure Regulator
- O2 Zirconia Oxygen Sensor
- Rugged Steel frame
- Exhaust Silencing Muffler
N2GC-2300 Controller
- 7” Color touch screen HMI interface
- Read Out’s
- Inlet Temperature
- Inlet Pressure
- Outlet Pressure
- Outlet N2 purity
- Alarm Setpoints / History
- Step Cycle
- Purity Control
- Telemetry Data Purity Trend
- Service Alarms
- Filtration element
- Desiccant Media
- Outputs 10+
Operating Voltage
- 110, 115 V / 1 PH / 50-60 HZ
- 230/208/220 V / 1 PH / 50-60 HZ –(Optional)
- 24 V DC- (Optional)
Power Consumption
- < 300 W
Pressure Vessel Certification
- ASME VIII, CRN
Control Panel Certification
- UL & CUL
Pre & Post Filtration Microns
- Control line Filtration Grade: 1.0 um
- Pre-Filtration Grade: .01 um
- Post Filtration Grade; 1 um
- Carbon Filtration Grade:.003 um
Inlet Pressure Rating
- Up to 175 PSIG
- Up to 12 BARG
Outlet Pressure Rating
- Up to 145 PSIG
- Up to 9.9 BARG
Operating Pressure
- 90 to 175 PSIG
- 2 to 12 BARG
Compressed Air Quality (Inlet)
- ISO 8573-1 Class 1-4-1
Nominal Sound Level
- <85 dB (A)
Electrical Enclosure Rating
- NEMA 4
Dew Point (Ambient Temperature)
- +40 ° F to -40 °F
- 4.4° C to -40° C
Min/Max Operating Temperature (Feed Air)
- 40/100 ° F
- 4.4/37.7° C
Min Ambient Temperature
- 38° F
- 3.3° C
Max Ambient Temperature
- 100° F
- 37.7° C
Flows & N2 Purity
- 95.000% (2.6-1,427 cfm)
- 96.000% (24 to 1301 cfm)
- 97.000% (21 to 1146 cfm)
- 98.000% (1.8 to 994 cfm)
- 99.000% (1.4 to 793 cfm)
- 99.500% (1.3 to 698 cfm)
- 99.900% (0.9 to 507 cfm)
- 99.950% (0.8 to 442 cfm)
- 99.990% (0.6 to 331 cfm)
- 99.999% (0.3 to 166 cfm)
N2P Series Models
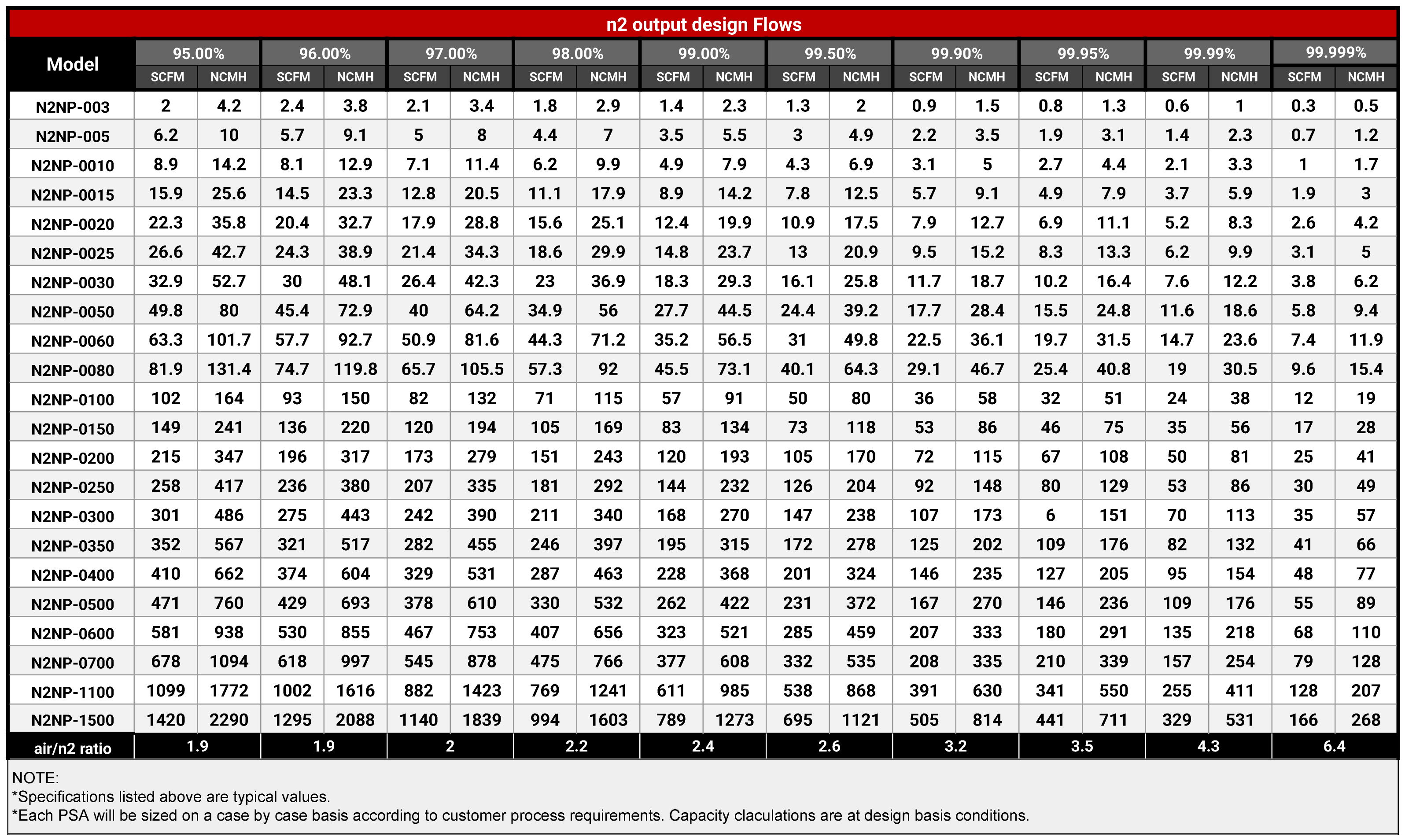
Correction Factors

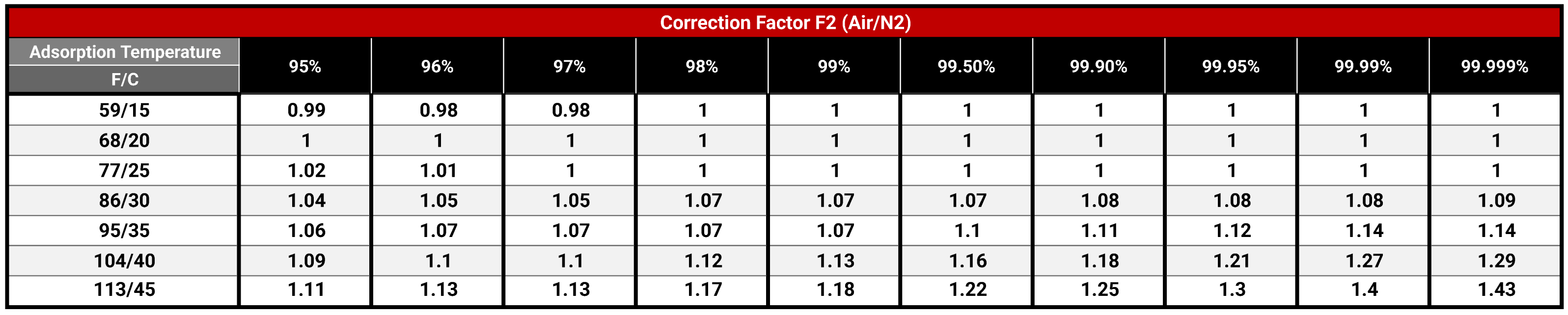
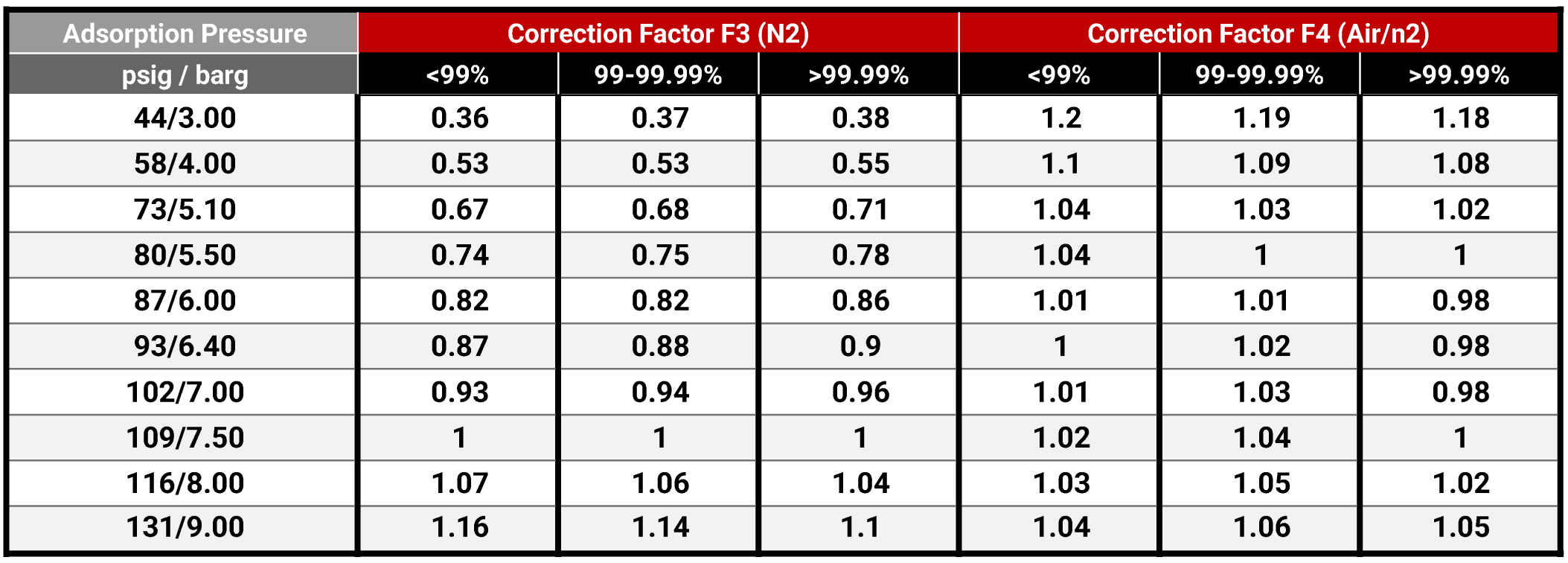
Dimensional Specifications
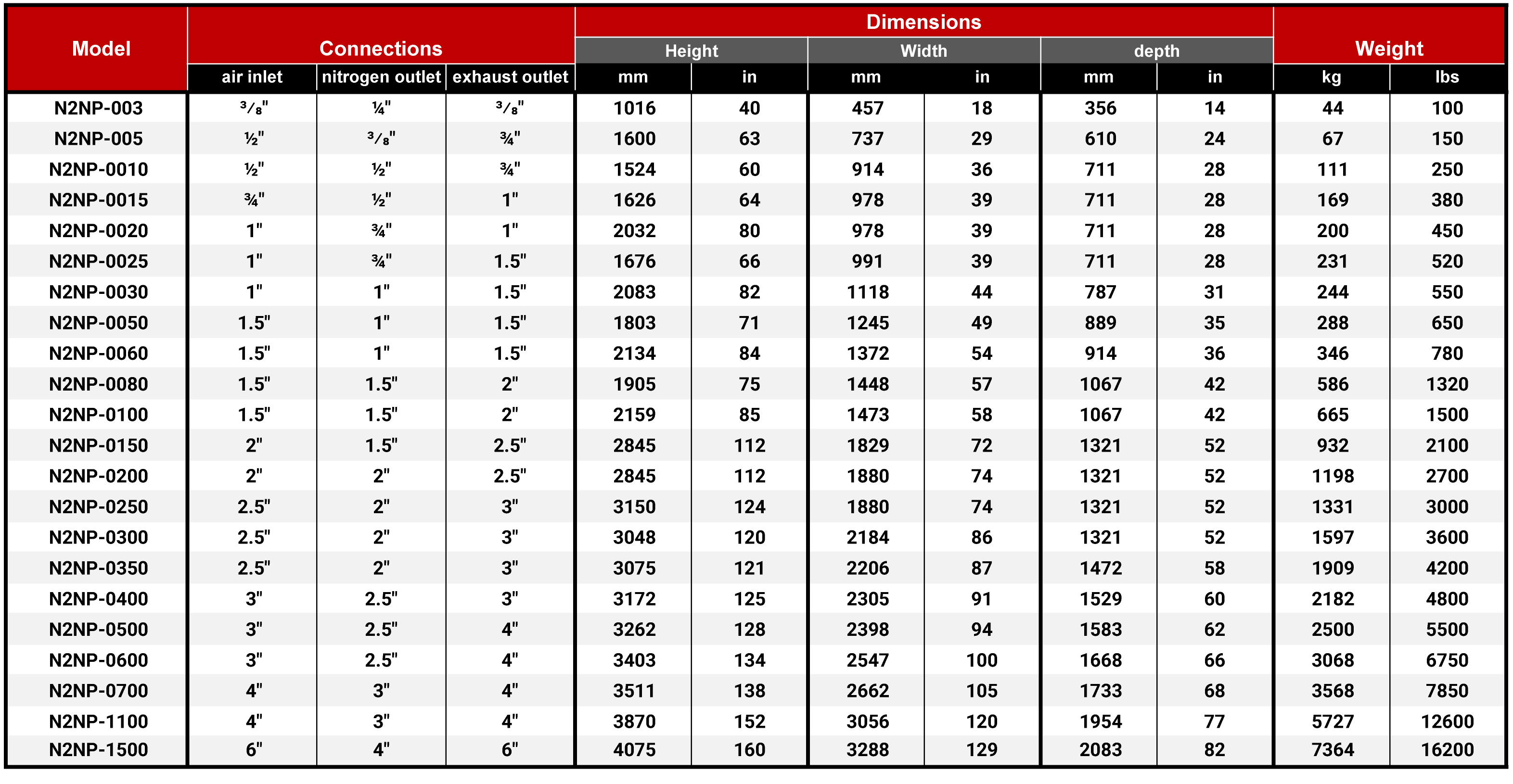
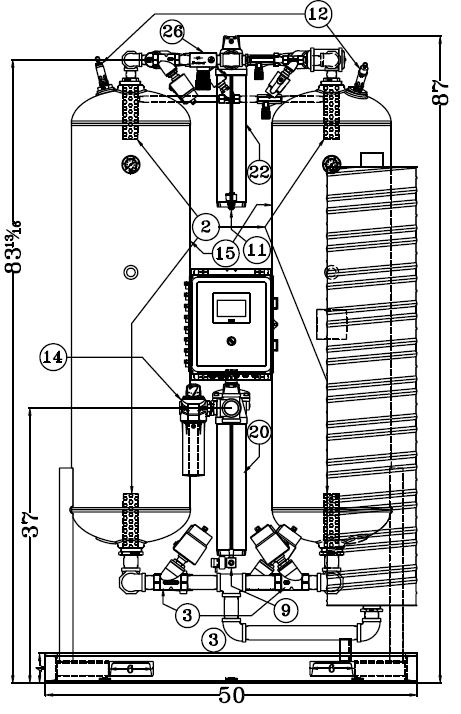
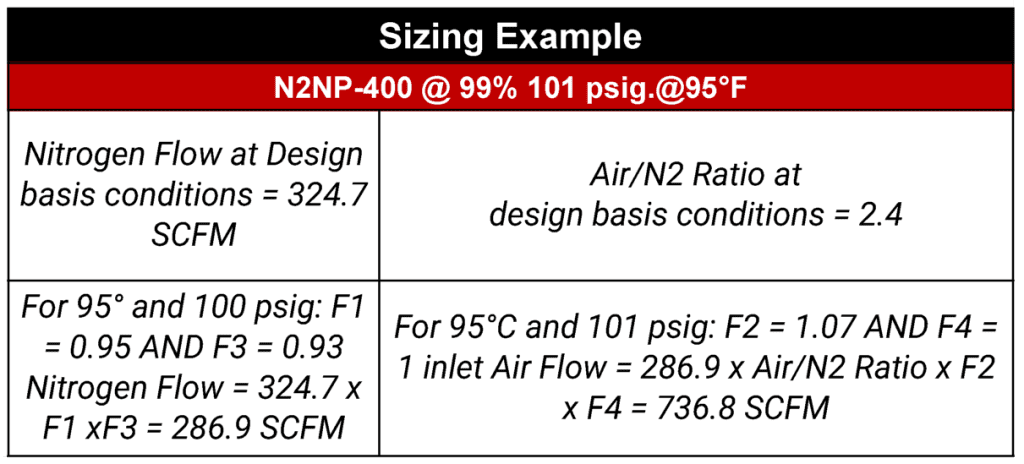
N2NP Optional Features
Optional FEATURES
(If an option is not listed, please contact our sales team to accommodate any additional options.)
ALTERNATE VOLTAGES:
- ALT-V-1: 208-230 VOLTS / 1 PHASE / 50-60 HZ
- ALT-V-2: 24 VOLT DC
ELECTRICAL ENCLOSURE:
- N4X-P: NEAMA 4X: POLYCARBONATE ELECTRICAL ENCLOSURE
- N4X: NEMA 4X: STAINLESS STEEL ELECTRICAL ENCLOSURE
- N7: NEMA 7 EXPLOSION PROOF
- EPH: Electrical Panel Heater
CONDENSATE DRAIN:
- EFD: EXTERNAL FLOAT DRAIN
- EZLD: ELECTRONIC ZERO LOSS DRAIN
- PZLD: PNEUMATIC ZERO LOSS DRAIN
- HPTD: HIGH PRESSURE TIMER DRAIN
DEW POINT & DIGITAL FUNCTIONS:
- DFM: Digital Flow Meter
- ESS: EMERGENCY STOP SWITCH
- RSS: REMOTE START / STOP
BYPASS:
- 3VBP: THREE VALVE BYPASS
FILTRATION:
- SP-F: SPECIAL FILTER CONFIGURATION
- FS: FILTER SKID
PACKAGES:
- HP: High Pressure
- RS: Rental Skid
- CS: Container packaging
CONSTRUCTION& ADD ON’s:
- CSA: CANADIAN STANDARDS ASSOCIATION
- BTS: BUILT TO SUIT
- IOPG: INLET-OUTLET PRESSURE GAUGE
- IOTG: INLET-OUTLET TEMPERATURE GAUGE
- TTG: TANK MOUNTED TEMPERATURE GAUGE
- VMI: VISUAL MOISTURE INDICATOR
- SST: STAINLESS STEEL CONTROL AIR TUBING
- NBT: N2 Buffer Tank
- ART: Air Receiver Tank
- Integrated Refrigerated Dryer
Your next step toward working with NEXT Air & Gas is to contact us for a Quote. Fill out the information below and give us the appropriate information needed to get started. Be sure to fill out all the contact information and our team will reach out with any questions or concerns.
If you’d rather speak to Sales Engineering, feel free to contact us at (865) 635-8178.
Below are links to product information and brochures. Please click and download at your convenience. If you have any questions or suggestions on materials you think would be helpful, please call us at (865) 635-8178.
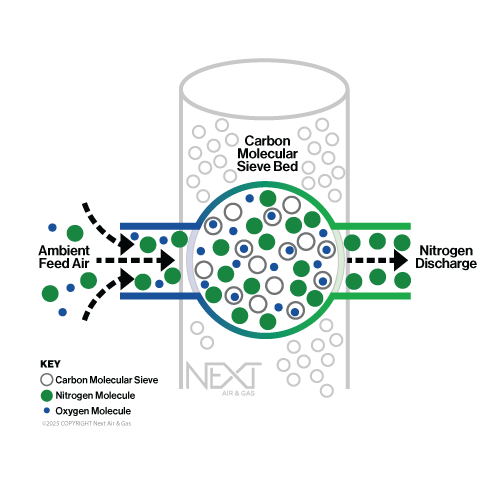
Principle of Operation
High n2 rates Next’s N2NP solution with PSA works under the principle of adsorption equilibrium and kinetic theory. Next’s kinetic adsorbent is highly selective to components such as O2 , CO2 and water vapor, while allowing nitrogen molecules to pass through the adsorbent bed. O2 , CO2 , and CO molecules easily diffuse inside the adsorbent pores when the bed pressurizes (adsorption). Nitrogen molecules, which have a larger diameter in comparison, cannot diffuse inside. The result is a purified nitrogen stream in the product. When depressurized (desorption), the adsorbed impurities are released through the exhaust port. Next’s PSA units consist of two identical beds filled with proprietary CMS adsorbents, connected. Compressed air feed enters the bottom of the first vessel. As O2, CO2 , water vapor and other trace contaminants stick to the adsorbents, the product stream leaves from the top of the vessel. When the adsorbent bed reaches the saturation point, it depressurizes and lets the desorbed gases move to the second vessel (equalization) at an intermediate pressure. This allows for a continuous production flow of nitrogen.

Step 1: Air compression & Pre-treatment
Atmospheric air must be compressed and treated to remove impurities before it enters the O2 removal process. Impurities include dust particles, traces of oil and VOCs compounds, low concentrations (parts per million) of CO2 , CO, and water.
Step 2: Dust & Oil removal
Oil-injected air compressors or oil-free compressors are used to pressurize atmospheric air. High humidity levels can compromise membranes and PSA performance; so, after compression, moisture levels are reduced using a refrigerant or desiccant dryer. When using refrigerant drying, condensate water is removed using a coalescing filter which also removes oil aerosols to 0.1 ppm and particles > 1µm. Condensate is eliminated from the system through an automatic drain. The gas is then reheated to about 68°F/20°C and passed through a combination of filters for dust and oil removal. In the case of desiccant dryers, adsorbed moisture is released into the exhaust stream from the dryer, and the dried air is passed through a particulate filter to remove particles > 1µm.
Step 3: o2 Removal
Dry compressed air is sent to an air receiver which reduces process fluctuations and guarantees smooth operation of the compressed air system and the O2 removal system. High efficiency coalescing filters are used to remove moisture and oil aerosols to 0.01 ppm and particles > 0.01µm. An activated carbon filter or tower is used for oil vapours and hydrocarbon odour removal to 0.003 ppm. At this point, the compressed air complies with ISO 8573.1 Class 1.4.1. When refrigerant dryers are used, or Class 1.1.1. when desiccant dryers are used. Nitrogen generation from air is accomplished by removal of O2 .
Overview

Applications
Our custom-designed nitrogen generation packages are mainly supplied for applications in the oil & gas, power generation, chemical, and mining industries. Our experience covers installations at desert or artic ambient conditions, as well as in classified areas.
nitrogen (n2 ) is a dry, inert, colorless, odorless gas. it is commonly used in a wide range of industry applications because it prevents both fast and slow oxidization.
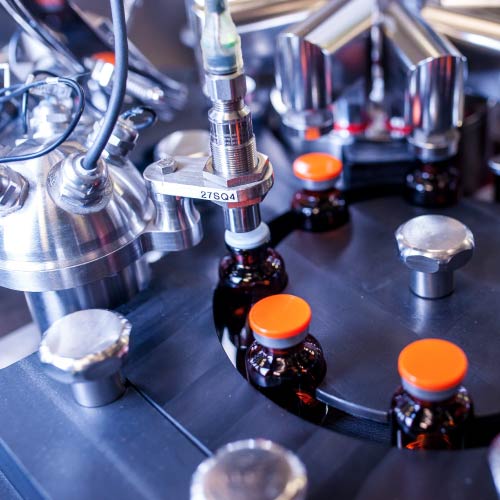
Blanketing
Due to its low reactivity, nitrogen is an excellent blanketing gas. Blanketing protects a product from the environment or vice versa. Blanketing is a common practice in the chemical, food, pharmaceutical, oil and gas, glass and metallurgical industries.
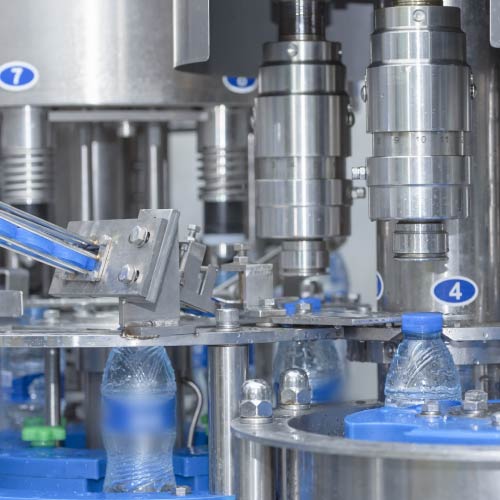
Modified atmosphere packing (Map)
The presence of oxygen inside packaged foods and beverages promotes bacterial growth and oxidation, compromising quality and shelf life. By flushing packaged foods with high purity nitrogen, oxygen levels can be reduced to below 1%. This technique is increasingly popular and represents an easy and economical way to protect products and improve package integrity.
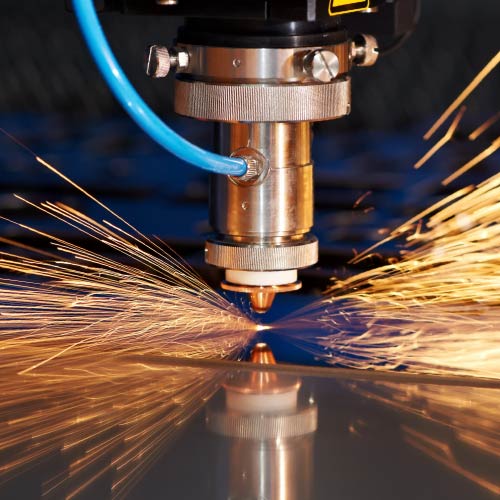
Metal Processing
A number of high temperature metallurgical processes are affected by contact with oxygen which favors the formation of oxides. By using nitrogen to minimize the oxygen contact, quality and operating cost can be optimized.
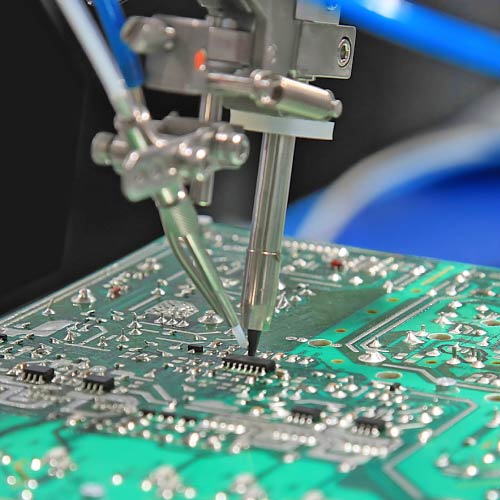
Electronics
The presence of oxygen and water vapor during electronic processing and packing can also lead to the formation of oxides which compromises yield and quality. Nitrogen is used to create inert areas around the process and soldering chambers.
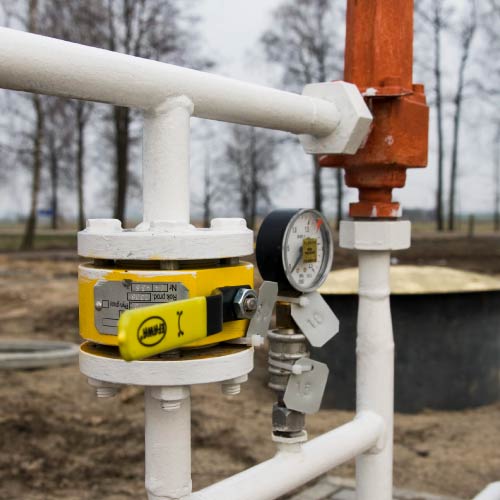
Oil and Gas Extraction
Inert gases such as nitrogen are commonly used in the oil and gas industry for gas lift. High pressure gases like nitrogen are injected into the tubing to reduce the density of the fluids. This allows for a reduction of flowing bottom hole pressure (BHP). Nitrogen is also used during electrical generation for blanketing the seals on natural gas compressors.