NXME Series (600-12,000 CFM)
High-Capacity Mist Eliminators
Next’s NXME Series Mist Eliminators are engineered and designed for exceptional performance under various load conditions, a long-lasting service life and durability in any environment. The NXME is the perfect solution for those who demand highly efficient filtration without compromising performance. Engineered to last over a decade, this range offers unparalleled protection for your oil-lubricated compressor, ensuring your system remains safeguarded even in the event of catastrophic failure. Built to the latest edition of VIII Div 1 ASME Code, our range is designed to be reliable and durable, providing the best possible performance while keeping operating costs low.
NXME Series Mist Eliminators have one of the lowest pressure drops available at 0.5 psi which is typically 4 psi lower than other industry conventional filters. This in return provides significant energy savings, as for every 2-psi pressure drop that is eliminated a 1% energy reduction in compressor horsepower is achieved.
NXME Series Features
- Very low pressure drop
- Large oil catching efficiency
- Easy field cleaning
- Positive sealing O-rings
- Auto Float Drain is standard
- Multiple drain style options available
- Removal of particles down to 0.01 micron including coalesced liquid water and oil providing a maximum remaining oil aerosol content of 0.01 ppm
- Increased surface area in a given volume allows low velocity separation of ultra fine oil mist.
- Elements are grounded to canister minimizing static electricity problems
- Achieves same high efficiency filtration as conventional downstream filters with a service life of 10+ years
- Typically located after an oil lubricated compressor to provide optimum protection in the result of a catastrophic failure of the compressor’s air/oil separator
- High efficiency and initial low pressure drop of less than 0.5 psig means units are utility rebate-friendly due to pleated media design v. conventional wrapped elements
- Heavy duty pressure vessel built in accordance with latest edition of VIII Div 1 ASME Code
- External powder epoxy coated as standard
- Zero air loss drain (shipped loose)
Design Operating Temperature Range
- 40 to 176 °F
- 4 to 80 °C
Design Operating Pressure Range
- 20 to 150 psig
Max Operating Pressure
- 200 psig
- 14 bar
Initial Differential Pressure
- less than 0.5 psig
Recommended Pressure Differential for Element Change
- 2.5 psig
- .17 bar
Filtration Performance
- 0.3 micron @ 99.97% efficiency
ISO Air Quality Class (solids, water, oil)
- ISO Class 2.7.3
NXME Series Range
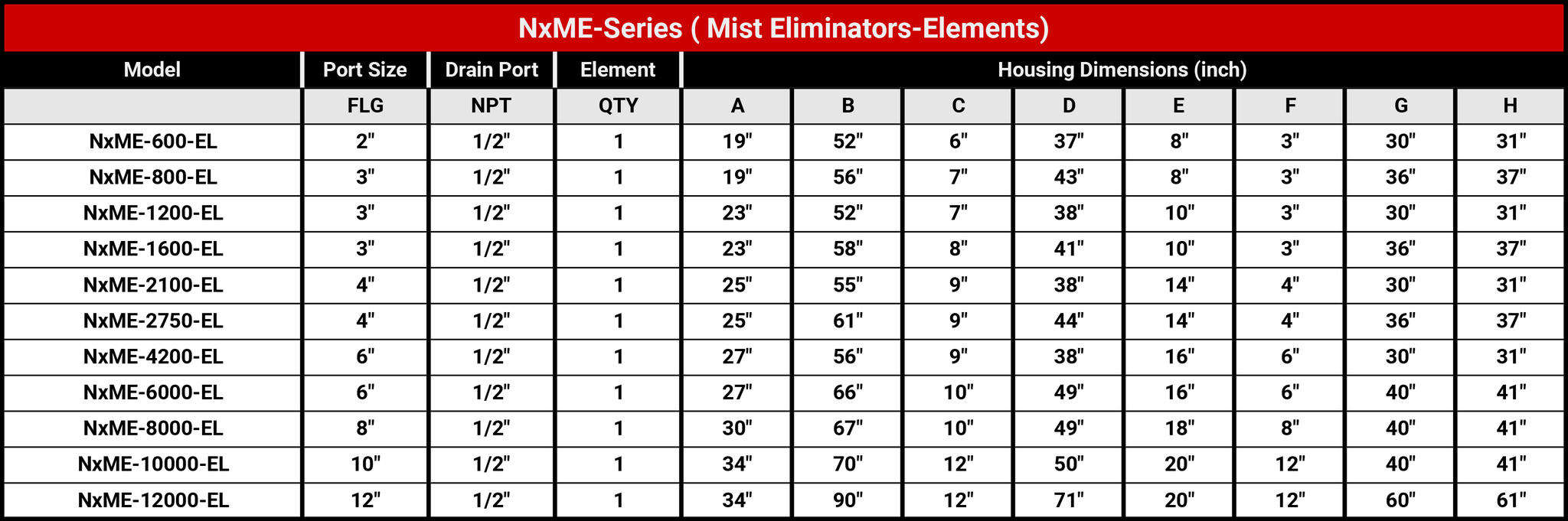
Correction Factors

For maximum flow rates, multiply model flow rate shown in the table above by the correction factor corresponding to the working pressure.
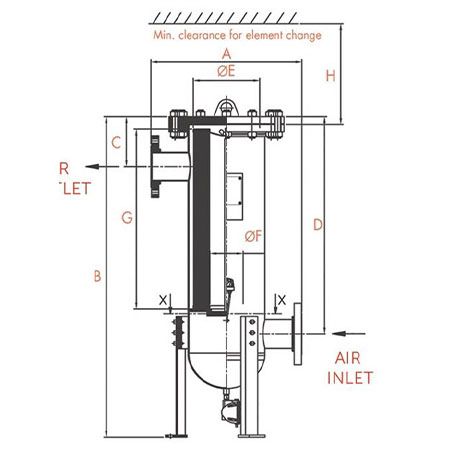
NXME Elements
- Ultra-low .05 psi differential
- High load factor compared to conventional hand packed media which is prone to poor performance under varying load conditions.
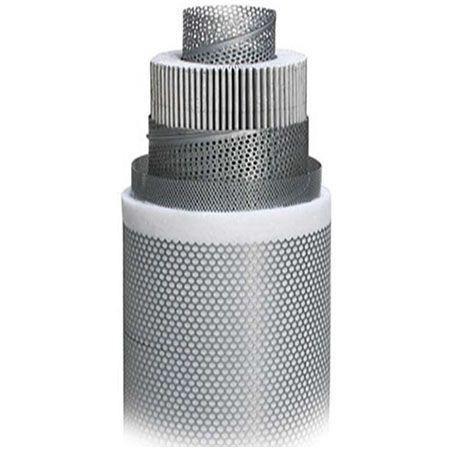
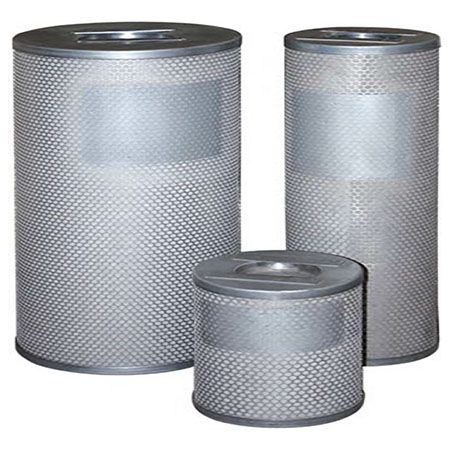
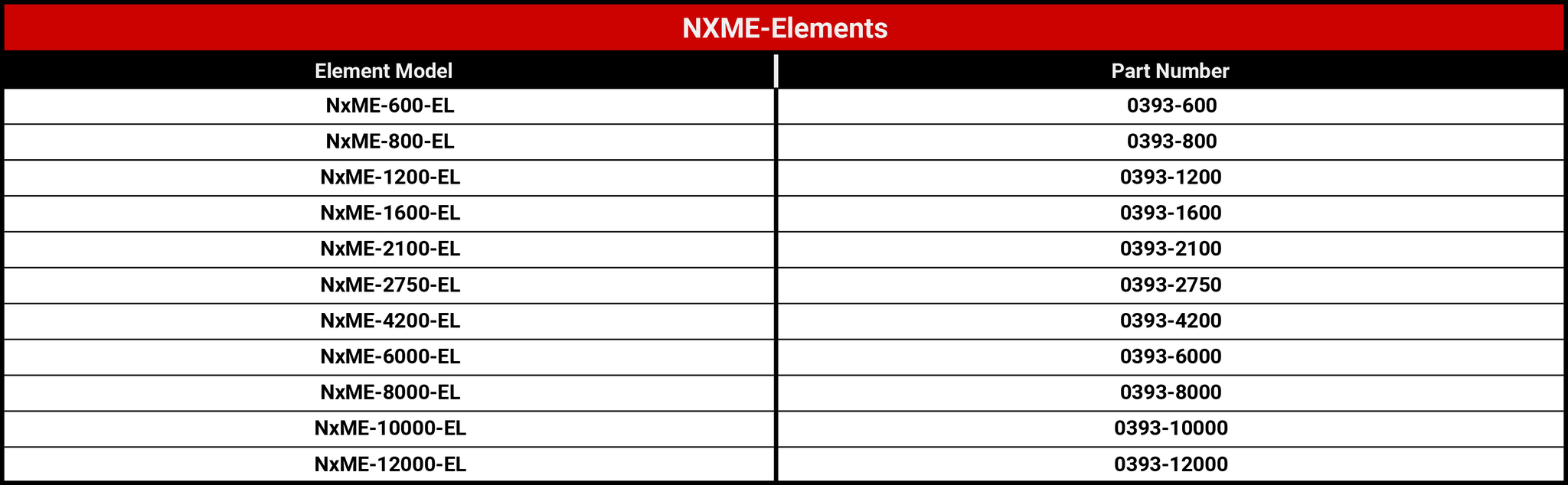
- Provides 9-10 times greater filtration surface area, greater dirt holding capability and lower pressure drop
- Eliminates migration of air flow to area of least resistance, also known as “channeling”
- Eliminates the shedding of media
- Consistent quality
- Strong Stainless steel support sleeve construction
- Eliminates rust and corrosion which can contaminate the air system
- Integral support of the filtration media to eliminate bypass of contaminants
- For the removal of particles down to 1 micron including coalesced liquid water and oil providing a maximum remaining oil aerosol content of 0.5 ppm
- Special machine pleated element construction
- The machined pleating of the filter media increases its stability under changing loads and reduces the specific surface tension
NXME Series Options
Next’s mist eliminators are equipped with an external float drain. As an option a NBM electronically, level-controlled zero loss drain can be fitted. The size of NBM is suited to the capacity of the mist eliminator and guarantees secure function even with high loads of condensate.
The Next condensate drain series, drain without the loss of compressed air, guarantees a secure and economical drainage of condensate for any application.
Electronic Zero Loss Drain
NBM- Series
Timer Condensate Drain
NTD- Series
Mechanical Zero Loss Drain
NWH- Series
Your next step toward working with NEXT Air & Gas is to contact us for a Quote. Fill out the information below and give us the appropriate information needed to get started. Be sure to fill out all the contact information and our team will reach out with any questions or concerns.
If you’d rather speak to Sales Engineering, feel free to contact us at (865) 635-8178.
Below are links to product information and brochures. Please click and download at your convenience. If you have any questions or suggestions on materials you think would be helpful, please call us at (865) 635-8178.
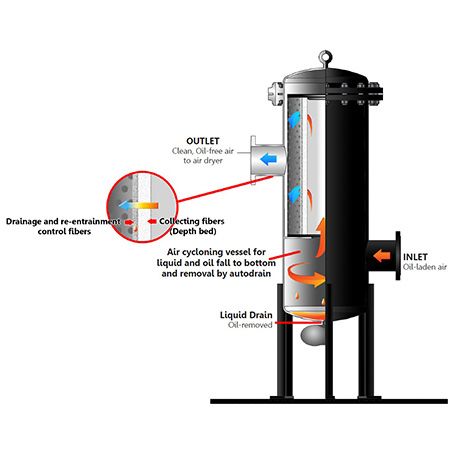
Principle of Operation
Compressed air is directed through a loosely packed bed of highly engineered, water resistant glass fibers. Water droplets and oil aerosols entrain in the air stream are captured by the fibers through the mechanisms of direct interception, inertial impaction and interception resulting in Brownian motion. The captured particles move along the fibers and coalesce into larger droplets that gravitate to the bottom of the element. Here they fall into a quiet zone in the bottom of the housing and are discharged from the system.
Overview
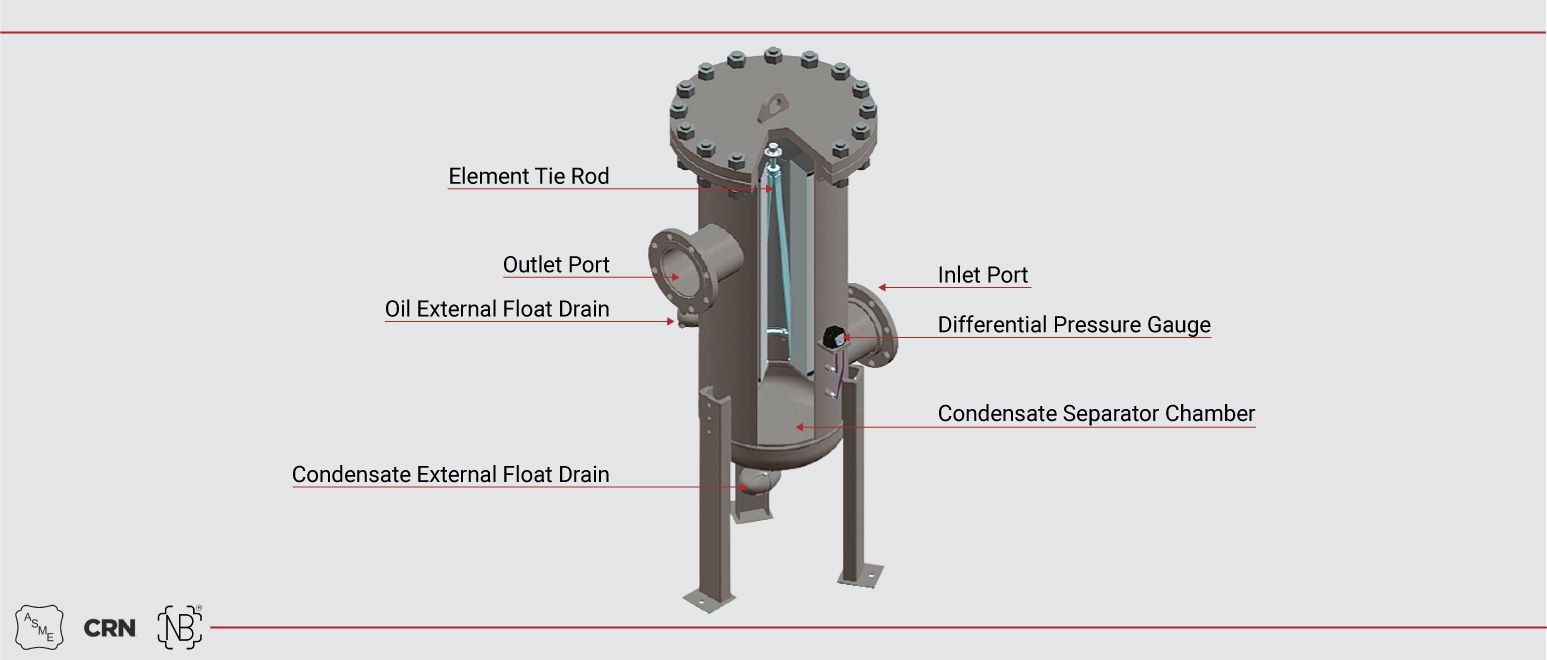

Design
The mist eliminator was designed to purify compressed air and oil, water and particles in the first purification line. The efficiency of the NXME is independent from operating pressure. Purification is made in three steps.
The first separation was made by gravity. Liquids and fluids are collected at the bottom of the filter housing. A special mist eliminator sieve is used in the second purification line and eliminates medium sized particles and liquid aerosols which will be led to the bottom of the filter housing. In the third stage, the purified air goes through specially treated ceramic elements, designed to remove the finest liquid and solid particles as small as 1 micron.
Due to treatment of the ceramic element, oil and water are repelled by the surface leading to a low pressure drop.
NxME Series Mist Eliminators are designed to meet the demand for:
- Efficient removal of oil-mist carryover from piston or oil flooded rotary compressors
- Long lasting service life
- Durable design to withstand strenuous operating conditions and environments
- Protection from oil slugs or compressor Air / Oil separator failure
Applications
- Capturing oil, Fog, Mist or Smoke From Exhaust and Pressure Unloading Vents on Oil Flooded Compressors, Vacuum Pumps and Blowers
- Applications Requiring Low Delta P Coalescing of Large Air Volumes
- Vacuum Freeze Drying
- Vacuum Out- Gassing and Vacuum Coating
- Food Processing
- Nailers / Staplers
- Industrial Vacuum Process
- Cement & Paper Processing
Why You Need a Mist Eliminator
Oil, solid particles, and moisture are the main problems of a compressed air system. By itself or in combination, they can plug the orifices of any pneumatic instrument, wear out seals, corrode system components, reduce the effectiveness of air operated tools, resulting in product rejection, lost production and most importantly- increased maintenance costs. All above problems can be avoided by using an efficient mist eliminator.
Contaminants
OIL: One of the most troublesome contaminants in a compressed air system is lubricating oil from compressors. Oil from a compressor enters the air stream in several forms: Liquid, vapor and aerosol. Usually, oil mist particles range from 20 to 0.01 micron in diameter. Compressor oil separator is only capable of removing large particles in liquid form, fine mists and oil vapor pass through to the downstream and must be removed by an effective low pressure drop mist eliminator.
SOLIDS: Dirt, dust and pollen are contained in the ambient air at the compressor intake. The atmosphere in a typical industrial area may contain a lot of dust particles and when they enter the intake of the compressor and compress it to 90- 100 PSI it has a ratio of one to eight. In other Words, it has eight times more contamination at 100 psi than in the atmosphere.
MOISTURE: Depending on the geographical area, ambient air contains moisture. As the compressed air leaves the compressor, its temperature increased due to the compression and when it gets cooled by an after cooler and the piping distribution it condense most of its moisture where it can cause rusting in pipelines and combine with oil and solid contaminant can form a sludge which can damage any device up stream.
PRESSURE DROP: One of the major factors in selecting a filter is pressure drop. Most of the coalescing filter’s element has pressure drop of 3 to 5 PSI based on the new dry filter to remove oil only, but as it was mentioned above, compressed air contains solids, and moisture and these increase the pressure drop and clog the filtration media. To improve the filter efficiency most manufacturers recommend additional pre-filter to remove particulates. While this extends element life the pressure drop increases and the operating cost of the air compressor increases.