NRD-VFD Series (500-5,000 CFM)
Cycling Refrigerated Dryers
The NEXT Pure-Stream NRD-VFD refrigerated dryer was designed with high efficiency, durability, and energy saving. The NRD-VFD utilizes the new and innovative PLC controller to turn the refrigerant compressor on and off based on actual speed conditions. The controller has been programmed to not only measure and respond to critical operating parameters, but to track and anticipate demand. This ability to proactively encounter speed changes and adjust the operating cycle accordingly sets the VFD series dryers apart from the competition.
The energy storage capacity of the aluminum plate heat exchanger ensures that VFD dryers can react quickly and avoid dew point spikes (sudden increases in dewpoint beyond acceptable limits) commonly associated with cycling dryers, while operating in the most energy efficient cycle. Over 35% of a dryer’s life cycle cost is the energy it consumes. To cut energy costs, we offer the VFD compressed air dryers with variable speed working cycle (Inverter).
The VFD range entails significant savings, reducing the consumption of energy that produces fuels and protecting the environment for future generations.
ADVANTAGES
- Greater Environmental friendliness,
- Reduced running Cost
- Optimized consumption and performance under all load conditions.
NRD-VFD Series Features
- Variable speed compressor from 20% to 110% of the capacity
- Energy accumulation function with compressor OFF with load lower than 20%
- Variable speed fan
- Equipped with electronic drain or programmable timer
- Internal, high efficiency separator
- Nema-1 Standard
- Programable timer drain
- Thermal Protection Switch
- Economical design
- Energy Savings
- Dual Sensor System
- Dew Point stability at 40° F / C
- Programmable Electronic Condensate drain
- Green sustainability focused R407C refrigerant
- Low pressure drops and energy efficient.
- Easy installation and start up.
- Hermetically sealed compressors
- Flat plate Aluminum Heat exchangers
Controller Features
- Touch screen HMI interface
- User Friendly
- Dew point monitoring
- Drain Management
- Alarm Management
- Energy Saving Consumption System
- Modbus Ready
Standard Operating Voltage
- 208-230 VOLTS / 1 PHASE / 50-60 HZ (500 cfm)
- 460 Volts / 1 Phase / 60 Hz (800 + cfm)
Electrical Certification
- UL, CUL
Refrigerant
- R407C
Max Operating Pressure
- 200 psig
- 14 bar
Min/Max Design Pressure
- 100-232 psig
- 7-16 bar
Inlet Air Temperature8
- 100° F /C
- 38° F /C
Max Operating Temperature
- 120° F
- 49° C
Max Ambient air Temperature
- 100°F
- 38° C
Standard Outlet Pressure Dew Point
- 36 to 39° F /C
- 2 to 4° C
Connection Type
- NPT (500-1500 cfm)
- FLG (2000+ cfm)
ISO CLASS DEW POINT CONDITIONS
- CLASS 4 (ISO 8573-1 )
NRD-VFD Series Models
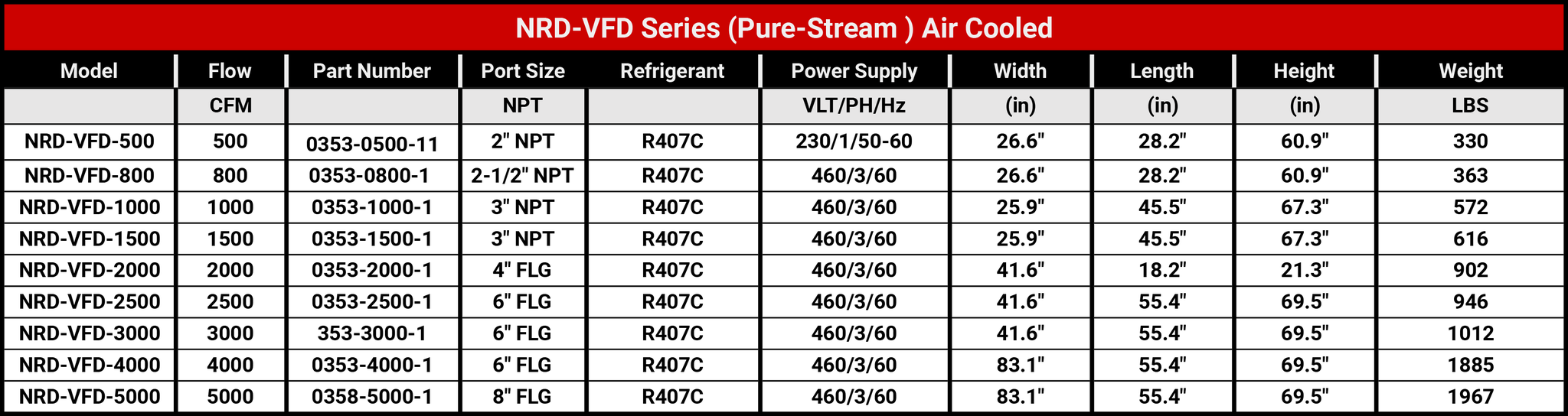
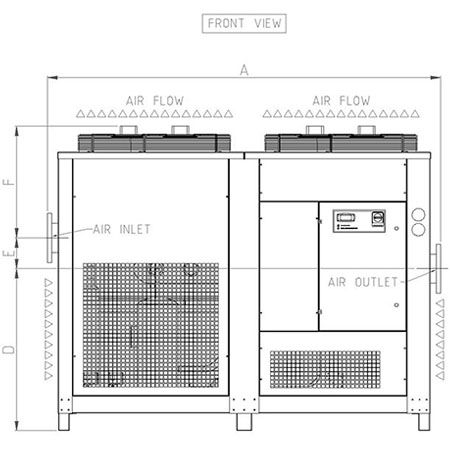
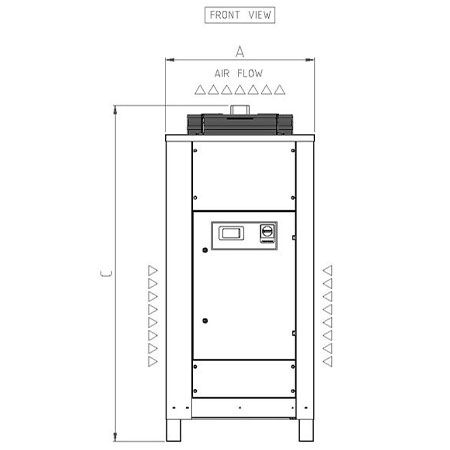
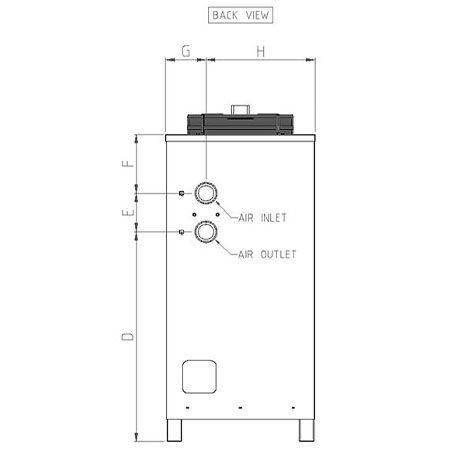
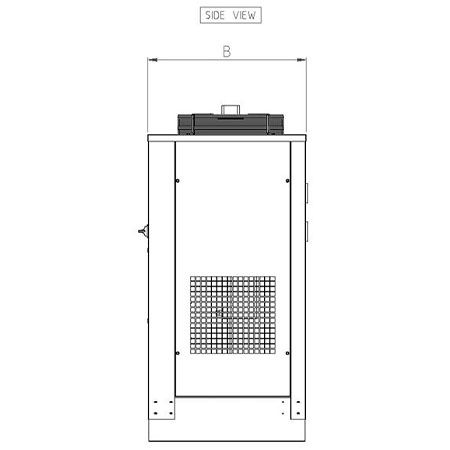
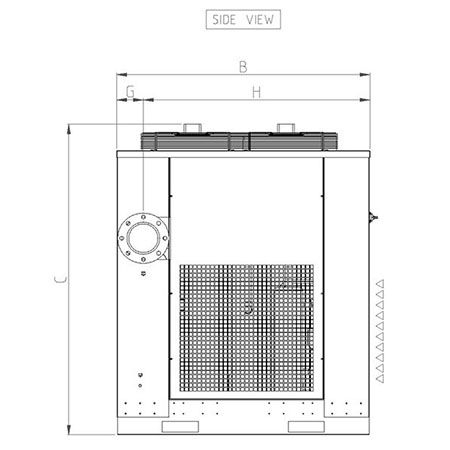
Correction Factors




Sizing:
Air flow capacity = Operating Pressure x Inlet air Temperature
NRD-VFD Optional Features
CONDENSATE MANAGEMENT+
NBM: Electronic Zero Loss Drain
NFD: External Zero Loss Drain
NTD-HP: High Pressure Timed Drain
FILTRATION+
PF: Pre filtration grade 0.01 μm
AF: After Filtration grade 1.0 μm
VOLTAGES+
ALT-VLT-230: 230/1/50-60
ALT-VLT-400: 400/3/50-60
CONSTRUCTION+
2VBP: Two Valve Bypass
3VBP: Three Valve Bypass
RERS: Rugged Enclosed Rental Skid
COOLING
NCP-W-1: Water Cooled (800-1600 cfm) Enclosed Frame
NCP-W-2: Water Cooled (2000+ cfm) Open Frame
*Please Note: The NCP-W series are engineered to order. Please contact the factory for additional information.
REGION SPECIFIC SPECIFICATIONS
(EMEA, LATIN AMERICA, ASIA, AUSTRALIA)
ALTERNATIVE VOLTAGES
- 230/1/50-60 & 400/3/56-60
ALTERNATIVE CONNECTIONS
- 2” BSP-F TO DN200
REGION CERTIFICATION
- CE, EAC,UKCA, CSA
Your next step toward working with NEXT Air & Gas is to contact us for a Quote. Fill out the information below and give us the appropriate information needed to get started. Be sure to fill out all the contact information and our team will reach out with any questions or concerns.
If you’d rather speak to Sales Engineering, feel free to contact us at (865) 635-8178.
Below are links to product information and brochures. Please click and download at your convenience. If you have any questions or suggestions on materials you think would be helpful, please call us at (865) 635-8178.
Principle of Operation
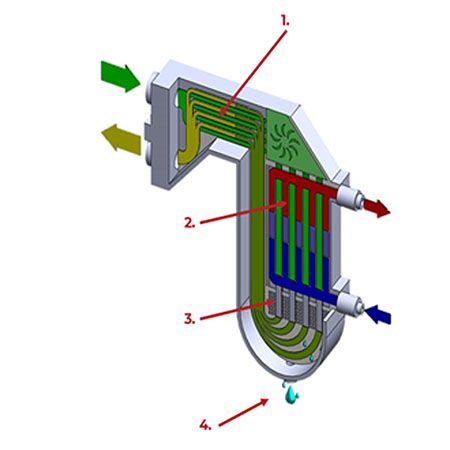
Moisture jeopardizes everything you want your compressed air system to do. Failure to remove this water ruins the product and fouls process. That’s why it is vital to have a reliable air treatment system in place to help protect your equipment and your operations.
Next Refrigerated Air Dryers reliably remove harmful moisture and contaminants from compressed air, helping protect your compressed air system, machinery and downstream tools.
- Saturated compressed air enters the system and is precooled in the air/air heat exchanger.
- Then, precooled air moves downstream through the air/refrigerant heat exchanger. The heat exchanger’s vertical profile design reduces condensed moisture by nearly 99% using gravitational force.
- To reliably prevent separated droplets from reentering the airstream, condensate collects in a large reservoir with subsequent recirculation where flow velocity is significantly reduced
- Accumulated condensate is then discharged from the dryer via drain. The dried, cold process air passes back through the heat exchanger to be reheated — reducing relative air humidity and recovering up to 60% cooling capacity.
Refrigeration Circuit
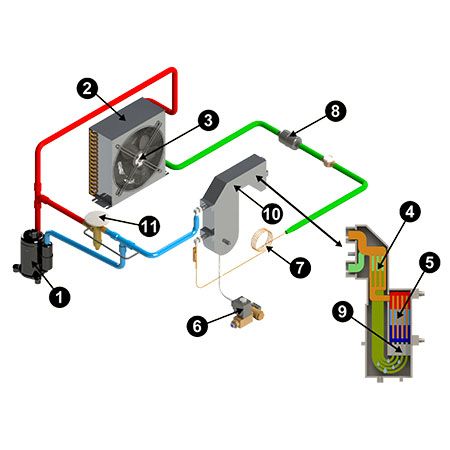
- Compressor
- Condenser
- Fan Motor
- Air to Air Heat Exchanger
- Evaporator
- Condensate Discharge ValveCapillary Tube
- Dryer Filter
- Demister
- Ultra Compact Heat Exchanger
- By-Pass Valve
Open View
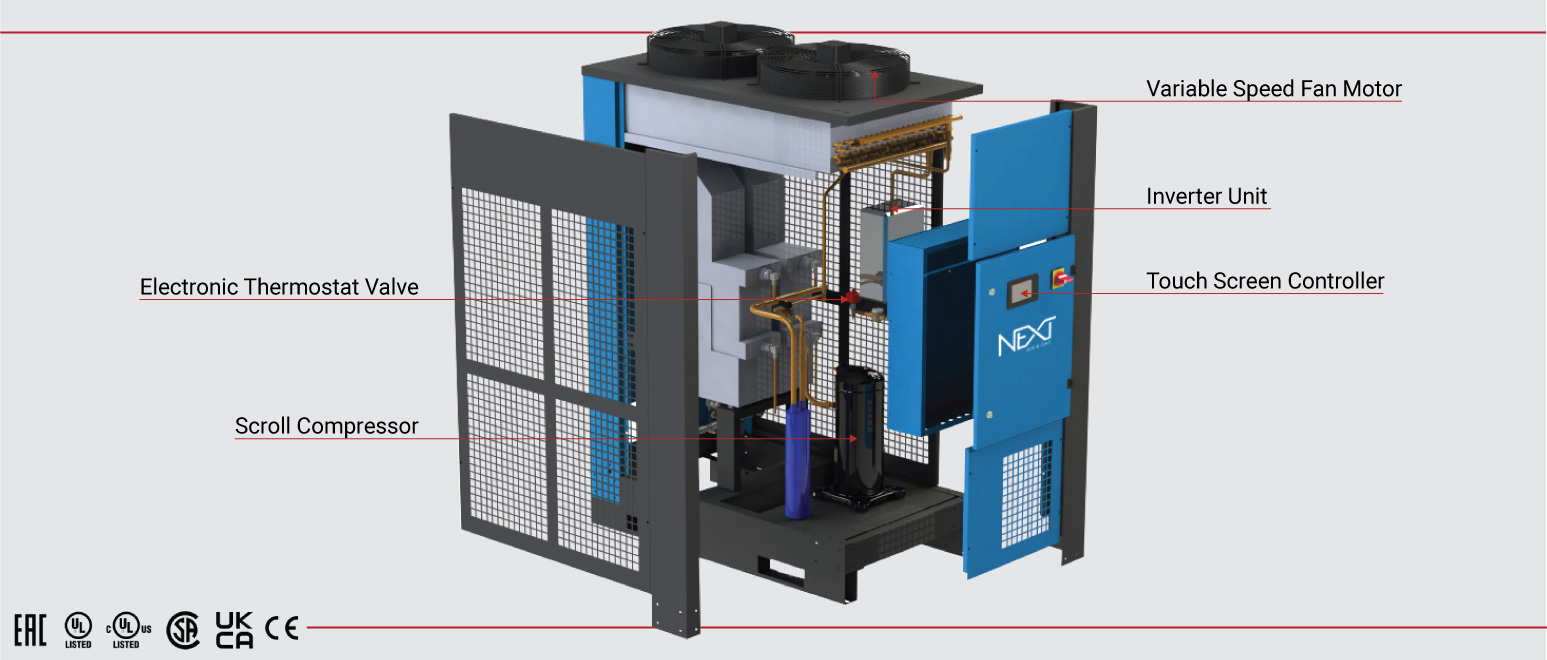
Next Air & Gas Performance Advantages
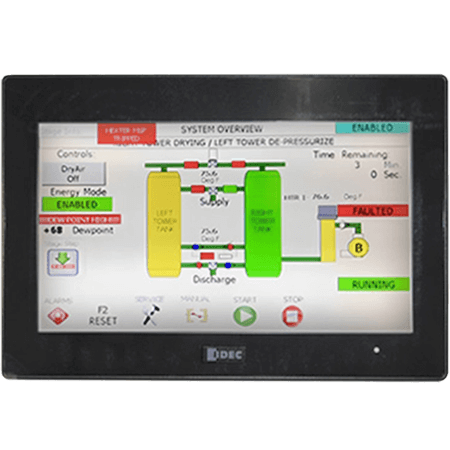
Controller
The NRD-VFD series is equipped with the HMI Touch Screen controller, which has an intuitive user interface with its 4.3” capacitive touch screen display and multiple functions. The controller constantly monitors and manages the operating pressure and temperature values and adjusts the compressor and fan speeds. This ensures an extremely stable dew-point under all operating conditions.
The controller’s main functions consist of:
- Operating Parameters
- Hour Meter
- Scheduled Maintenance
- Alarm Management
- Energy Savings Management
- Drain Management
- Dryer management via Modbus RS485 RTU Communication
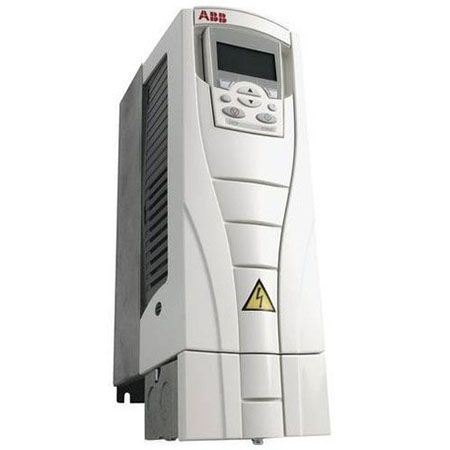
Variable Frequency Speed Drive
Variable speed dryers, using inverter technology for compressors and fans, can adapt their energy consumption according to the thermal load applied, and adjust the refrigerant flow rate to the heat exchanger. With the Touch Screen controller and electronic hot gas bypass valve, the user can choose between Cycling or No-Cycling operation for extremely low heat loads. The VFD feature on the dryer allows the refrigeration compressor to speed up and slow down to meet periods of both high and low demands, without using any excess energy.
- Energy Savings While providing optimum performance under all operating conditions, the standard dryer (fixed speed) has a regular energy consumption even under reduced load conditions.
- Precision Dewpoint The dryer operates off a set target dewpoint rather than cycling between a range of refrigerant pressures. This produces consistent dew points which means consistent production results.
- Soft Motor Starts–As opposed to full voltage motor starts on most fixed speed dryers, the VFD drive initiates slow motor starts which significantly lowers the electrical demand. Up to 75% turndown allows for a wide range of efficiency
- Reduced Power Consumption – Unlike a standard dryer, Kw consumption stays on par with your compressed air dew point demand, resulting in significant energy
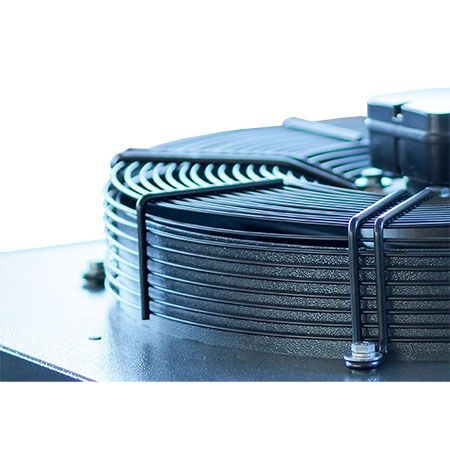
Variable Speed Drive Fan
The condenser fan on the dryer is also controlled with a variable speed drive. This allows for the condenser fan to speed up and slow down as refrigerant pressure changes, thus saving energy costs.
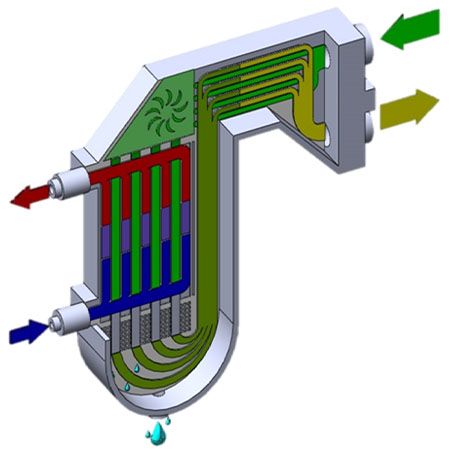
Vertical Heat Exchange Design
The patented aluminum heat exchanger has been designed to offer maximum performance and minimum pressure drop. The unique heat exchanger is both an air-to-air heat exchanger as well as an air to refrigeration heat exchanger. The warm and humid air is pre-cooled by the cool dry air that is leaving the dryer, which increases efficiency.
The air-to-air and the air-to-refrigerant heat exchangers plus the demister type condensate separator are housed in a unique module. The module has a vertical flow layout ensuring a natural facilitated down flow of the wet compressed air to the condensate drain. The counter flows of compressed air ensure maximum heat transfer.
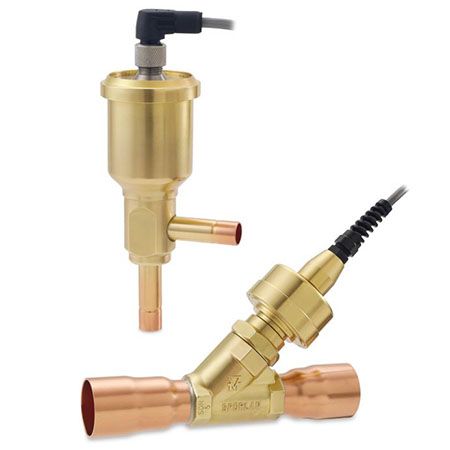
Hot Gas Bypass Valve
The precise and accurate electronic hot gas bypass valve prevents the formation of ice inside the evaporator at any load condition. The valve is set during the final test and no further adjustments are required.
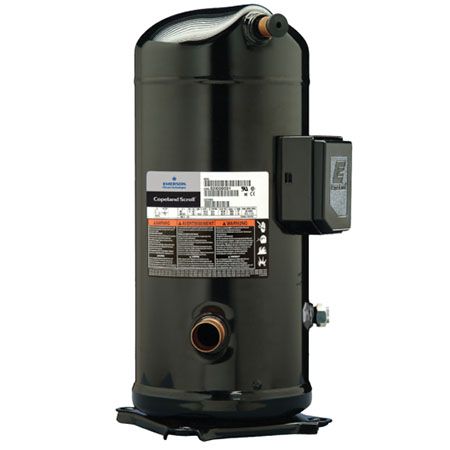
Scroll Refrigeration Compressor
The circulation of the refrigerant in the cooling system is done through the highly efficient refrigerant Scroll compressor. Thanks to its innovative construction, this has reduced energy consumption and increased reliability levels.
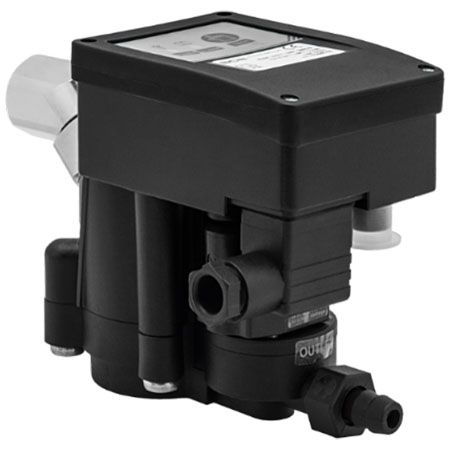
Zero Loss Condensate Drain Controls
To achieve additional energy savings, the VFD dryers are equipped with an electronic zero loss drain which is controlled by the controller, which prevents the expulsion of compressed air together with condensed water. The Electronic Zero Loss Drain accumulates condensate without any loss of compressed air, reducing energy costs and CO2 emissions. This is possible due to the integrated capacitive sensor and intelligent electronic system that manages drainage of the correct amount of condensate.