NFX Series (45-1,600 CFM)
Standard Pressure Filtration
NEXT’s NFX filtration line protects your plant equipment and processes, improves your product quality, and reduces your energy costs. Our NFX series filters are equipped with all the features required to make this the most efficient and cost-effective filter for your compressed air system. It’s a 2-part permeant pressure cast molded aluminum housing; that goes through the process of anodizing Low-pressure drop is achieved through optimal flow path design. The high efficiency bowl and non-turbulent lower filter zone assure that no condensate gets re-entrained in the air stream. The NFX differential pressure gauge notifies maintenance personnel of the optimal point at which to change filter elements. The added option of our AQUA-PURE electronic drain series assures that no compressed air is lost when liquid condensate is drained
NEXT offers filtration products in an application range from general purpose air to the most stringent food and pharmaceutical applications. Next’s NFX filters are available from 45 to 1600 cfm, @ 290 Psig, and design temperatures of 35 °F (2°C) to 350 °F (177°C).
- Engineered for energy efficiency – helps reduce operating costs
- Durable Housing construction for corrosion resistance
- Broad filtration from general purpose to highly stringent applications
- Optimized air flow design to help increase efficiency and reduce pressure loss
- Built for reliable and easy maintenance
The Next range of compressed air filters is designed from the outset to meet current and forthcoming requirements for compressed air quality. Using aerospace technology, Next has optimized the flow path through the housing and element, significantly reducing air turbulence and pressure losses. Providing an optimal flow path is key to reducing pressure drop and system operating costs.
NFX Series Features
- The air filters have five (5) ranges of efficiencies, removing contaminants as small as 0.01 micron at up to 290 psi -1/2″ to 3′ NPT/BSP pipe sizes.
- A protected auto float drain (0.07″ orifice) is standard for optimal and reliable removal of liquid contaminants.
- These air filters have zero-porosity aluminum and durable epoxy powder-coat finish, along with a corrosion resistant internal coating for a long service life.
- Filter combinations are configured to meet specific application requirements.
- Filters comply with pressure Equipment directives and perform as per related Iso 8573 standards.
- Filters are equipped with differential pressure gauges for ease of maintenance and energy efficiency.
- Superior filtration from 1 micron to .01 micron
- Durable element construction
- Efficient drain layer ensures continued performance after optimal element change periods
Max Operating Pressure
- 290 Psig
- 19.9 Bar
Flow Rates
- 45 – 1,500 SCFM
Connections
- 1/2” NPT TO 3” FLG
Min/Max Operating Temp Range
- 35 to 250°F / 1.5 to 121°C
- 350°F / 176°C (FRHT- High Temp)
Material
- Anodized Aluminum
ISO air quality class (solids, water, oil)
- ISO Class 8573-1
Certified
- CRN
NFX Series Range
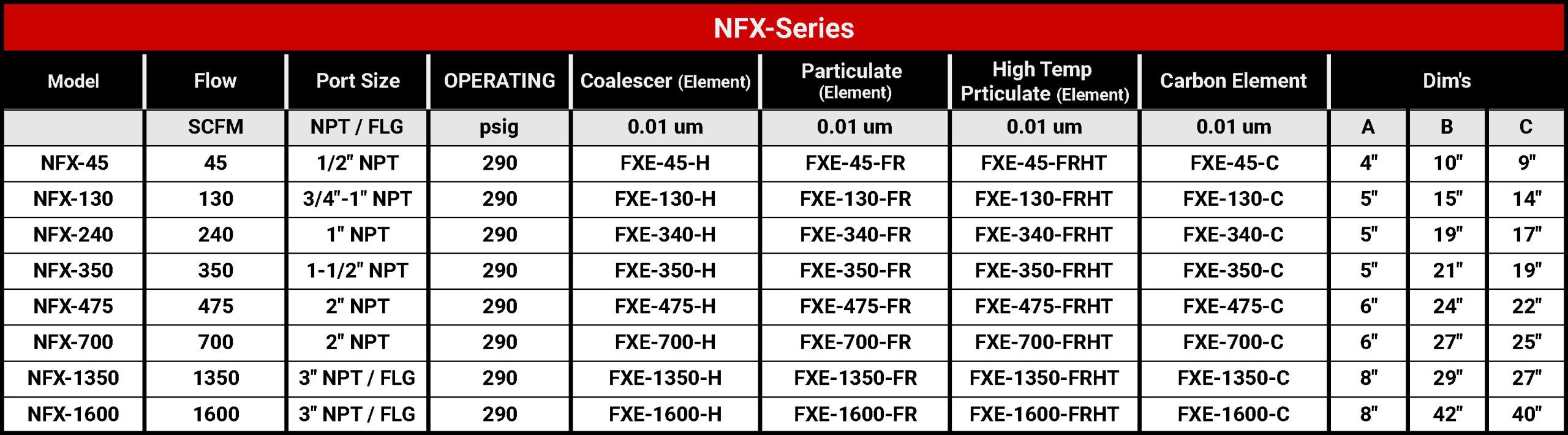
Correction Factors

For maximum flow rate, multiply model flow rate by the corresponding working pressure correction factor.
Correction Sample:
If a compressor delivers 500 scfm at 160 psi please choose your filter model as follows: (500 scfm / 1.25) = 400 scfm, Therefore a NFX-475 would be needed.
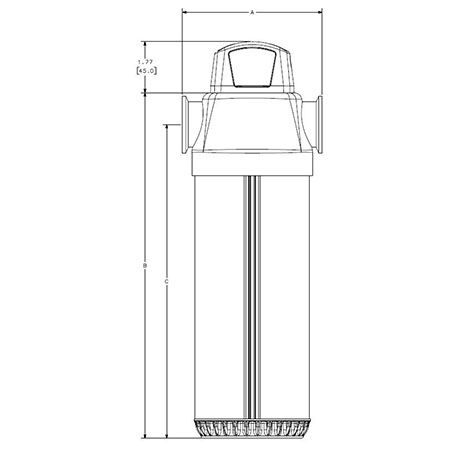
NFX Elements
Particulate: F and FR Elements
High Efficiency filters remove particles to 1 micron, including coalesced liquid water and lubricants
- Maximum Remaining aerosol content after filtration 0.5 ppm at 70°F (21°C)
- Media Type
- Pleated
- Efficiency Performance:
- (F) 1 micron & 0.5 ppm carryover
- (FR) Reverse 1 micron & 0.5ppm carryover
- Flow Direction
- (F) In-to-Out
- (FR) Out-to-In
- Dry Pressure Drop (psig)
- (F) 0.6
- (FR) 0.35
- Wet Pressure Drop (psig)
- (F) 1.2
- (FR) 0.6
- ISO Class
- Class 2: ISO8573-1
- Type of Filtration
- Particulate
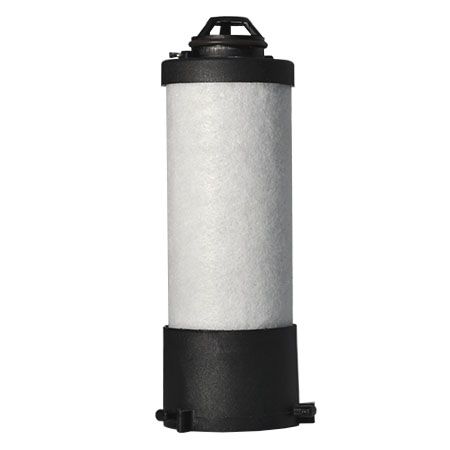
High Efficiency Coalescing: H and HR Elements
- Maximum filtration to remove particulate down to 0.01 micron, including water and oil aerosols. Maximum remaining oil aerosol content of 0.01 ppm at 70°F (21°C), when used with Next particulate filters.
- Media Type
- Pleated
- Efficiency Performance:
- (H) 1 micron & 0.01 ppm carryover
- (HR) Reverse 0.01 micron & 0.5ppm carryover
- Flow Direction
- (H) In-to-Out
- (HR) Out-to-In
- Dry Pressure Drop (psig)
- (H) 1.2
- (HR) 4.5
- Wet Pressure Drop (psig)
- (H) 2.3
- (HR) 0.7
- ISO Class
- Class 1: ISO8573-1
- Type of Filtration
- Coalescing
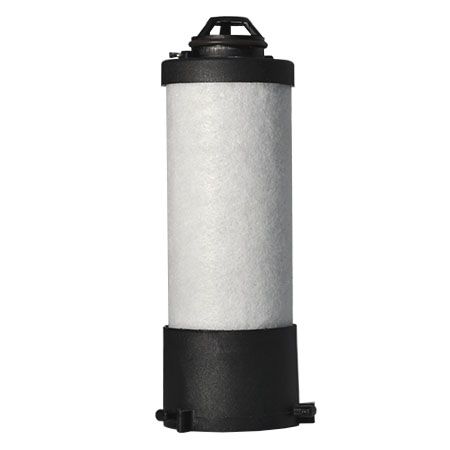
Vapor Removal: C Elements
- Filters with activated carbon remove lubricant and hydrocarbon odors
- Remaining vapor content is less than 0.003 ppm (excluding methane)
- This filter installation should always be preceded by high efficiency filter grades
- Media Type
- Granule
- Efficiency Performance:
- 0.01 micron & .003 ppm carryover
- Flow Direction
- Out-to-In
- Dry Pressure Drop (psig)
- 2.3
- Wet Pressure Drop (psig)
- 2.3
- ISO Class
- Class 1: ISO8573-1
- Type of Filtration
- Carbon
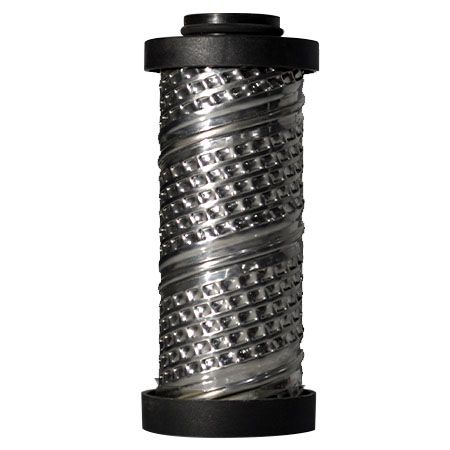
High Temperature: FRHT & HT Element
- Filters are available for temperatures up to 350°F (176.6°C)
- FRHT- High efficiency particulate filter elements.
- Media Type
- Pleated
- Efficiency Performance:
- High Temperature Reverse 1 micron & 0.5 ppm carryover
- Flow Direction
- Out-to-In
- Dry Pressure Drop (psig)
- 0.35
- Wet Pressure Drop (psig)
- 0.6
- ISO Class
- Class 2: ISO8573-1
- Type of Filtration
- Coalescing
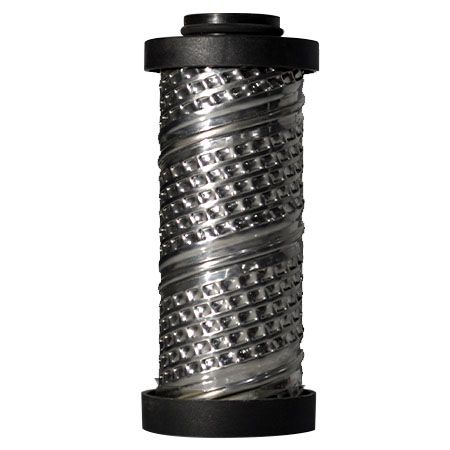
Ultra Filter: U Element
- For sensitive and high-end applications including pharmaceutical grade, Next offers the Ultra Filter, an absolute high efficiency particulate filter. (0.01 Micron Absolute)
- Media Type
- Wrapped
- Efficiency Performance:
- 0.01 micron absolute
- Flow Direction
- Out-to-In
- Dry Pressure Drop (psig)
- 5
- Wet Pressure Drop (psig)
- absolute
- Type of Filtration
- Particulate
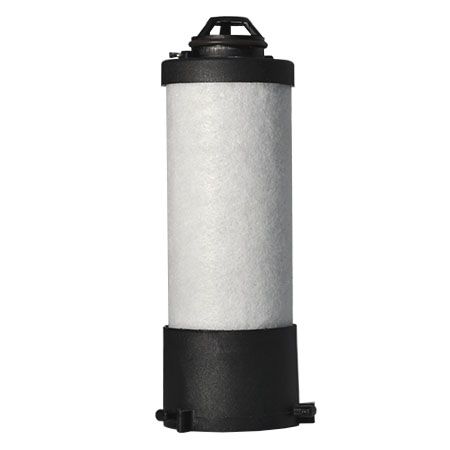
Filter Media Designed for Compressed Air
High quality compressed air filtration starts with selecting the correct filter media. Next uses superior-quality filter media with a new hybrid technology. Our elements stop the perpetual discussion about the use of filter media with or without binders because they are layered with body types, tailored to the filtration task. This neutralizes the inherent disadvantages and, as a result, retains the advantages of both types. The fine filter media is protected on both sides using a supporting fabric to increase both the stability and reliability.
Pleated Filter Elements
Pleated filter elements provide significantly greater filtration area than non-pleated. The higher filter area provides more void space for holding contaminants which reduces the differential pressure caused by retention of solid particles. The service life of the filter element increases proportionally which results in operating and maintenance cost savings.
Incorporated Drainage Media
The filter and drainage media are supported between two stainless steel supporting cylinders, eliminating any potential detachment of the filter media. The drainage media is located inside the filter element, eliminating potential handling damage. The stainless-steel cylinders have big, diamond-shaped openings for optimum flow conditions. Compared to punch-hole versions, their contribution to differential pressure is much lower and they are much more environmentally friendly because they are made from expanded sheet metal, i.e. without metal scrap.
Two-stage dry type Separation
During dry-type separation without-to-inside flow through the filter elements, the drainage media functions as a pre-filter stage, preventing coarse contaminants from entering the fine filter media. As a result, the differential pressure caused by contaminants is reduced and the service life of the filter is extended. As an additional advantage, the filter elements can also be used for wet type filtration.
Abrasion-free Activated Carbon Filter with 100% Activated Carbon
Both the filter element type and the cartridge type contain pure activated carbon granulate. The increased filling quantities contribute to a high separation performance and a long service life. Both the elements and the cartridges have an integrated general purpose filter element which significantly reduces the abrasion particles of the activated carbon. As a result, downstream dust filtration is not required, reducing installation, operation and maintenance costs.
NFX Series Options
The Next condensate drain series, drains without the loss of compressed air and guarantees a secure and economical drainage of condensate for any application.
The sizing of the condensate drains matches perfectly the volume flows and guarantees secure drainage even with higher condensate volumes.
Electronic Zero Loss Drain
NBM- Series
Timer Condensate Drain
NTD- Series
Mechanical Zero Loss Drain
NWH- Series
External Zero Loss Float Drain
NFD- Series
Your next step toward working with NEXT Air & Gas is to contact us for a Quote. Fill out the information below and give us the appropriate information needed to get started. Be sure to fill out all the contact information and our team will reach out with any questions or concerns.
If you’d rather speak to Sales Engineering, feel free to contact us at (865) 635-8178.
Below are links to product information and brochures. Please click and download at your convenience. If you have any questions or suggestions on materials you think would be helpful, please call us at (865) 635-8178.
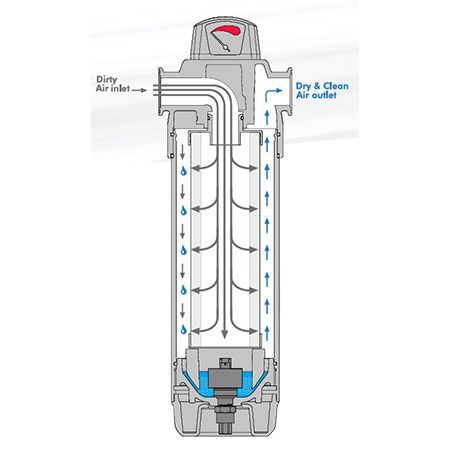
Principle of Operation
Contaminants are introduced at various stages of the air compression cycle. Removing these contaminants is vital to help ensure part quality, avoid machine damage and protect the air stream.
- Compressed air enters the filter housing inlet. The inlet design helps optimize airflow as compressed air moves into the physical medium of a filter element.
- Then, Untreated compressed air passes through filter material designed for retention of particles such as liquid oil, oil aerosols, dirt and scale.
- Finally, the treated, clean compressed air flows down stream to other inline components or point of use.
- Removed condensate moves from the treated air to be easily drained.
Open View
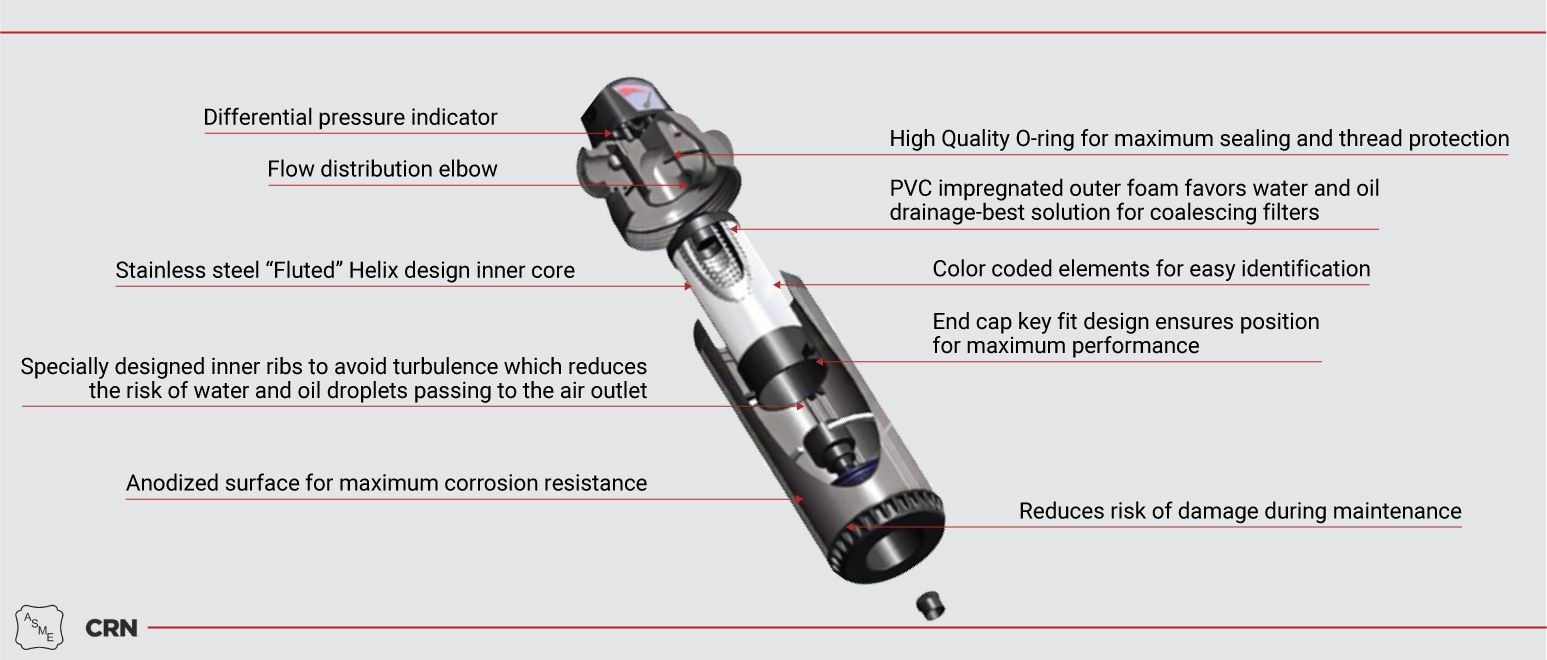
Next Air & Gas Performance Advantages
The performance of any desiccant dryer depends on the quality of its key components. Next Air & Gas uses the best available valves, controllers and desiccant. With accurately designed and sized components, the dryers are manufactured to provide you with years of trouble-free operation.
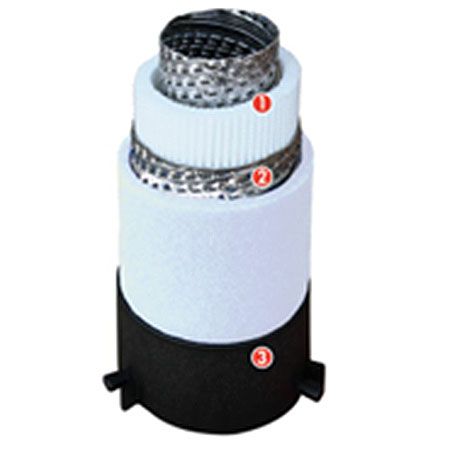
Pleated Element Design
1. Deep pleating enables a lower pressure drop.
2. Supreme collapse resistance due to strength of fluted stainless tube design protecting provides strength against pressure drops while improving the performance by passing air diagonally through the element.
3. PVC impregnated foam assists Water/Oil drainage.
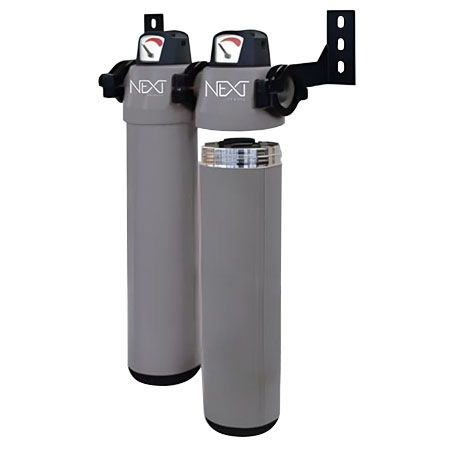
Series Integration
Head Clamping provides serial connection of filters without any extra piping.
Zero Clearance
A Major innovation is the use of a zero-clearance design. Provides for a simple element change without usage of tools.
Corrosion Resistance
Anodizing proves supreme corrosion resistance. Anodized surface treatment is proven to be better than other surface treatment methods such as Alo-chrome coating.
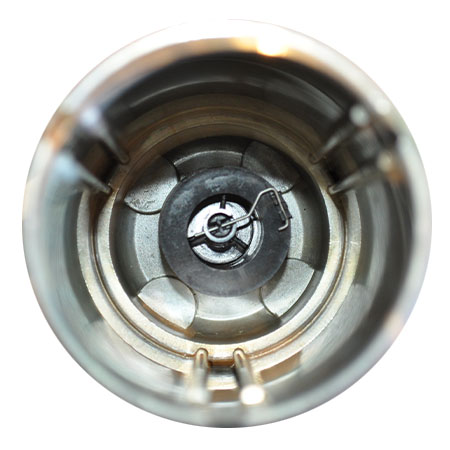
Drainage Ribs
Anodizing proves supreme corrosion resistance. Anodized surface treatment is proven to be better than other surface treatment methods such as Alo-chrome coating.
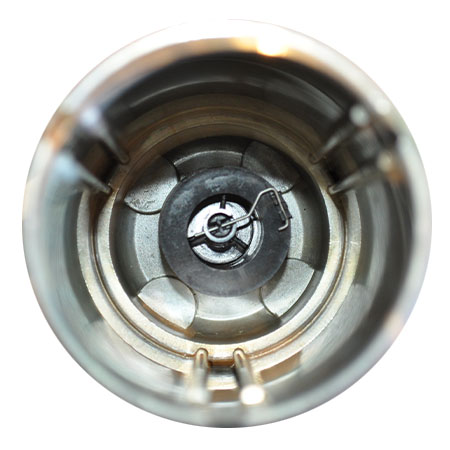
Deep Bed Pleating
For particle and aerosol removal, deep bed pleating provides 450% more filter media than an ordinary element, giving a larger filtration area, lower flow velocities, increased dirt holding capacity, lower running costs and a more compact filter element. Graded density further improves filter life and overall performance.
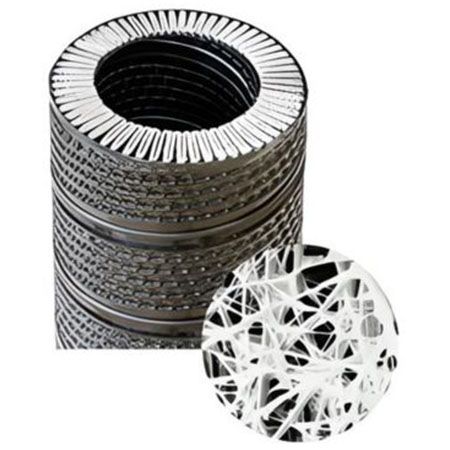
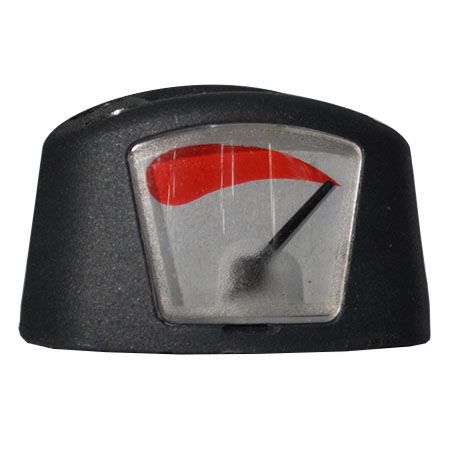
DP-GAUGE
A high-quality differential pressure indicator is used to identify pressure differential.
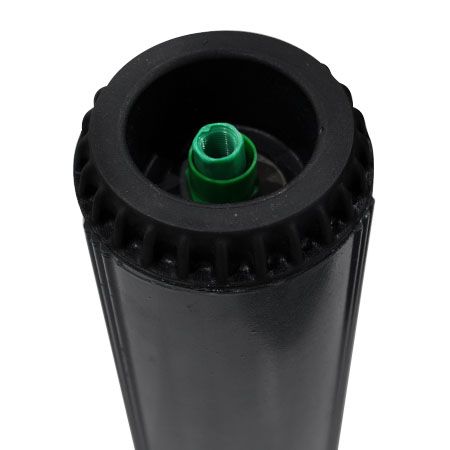
Recessed Float Drain
A specially designed auto drain system protects the auto drain against damage during shipping, handling and installation.
Next’s Compressed Air & Gas Filtration
The need to effectively and efficiently dry and filter compressed air & gas cannot be overemphasized. Ineffective purification can lead to system and / or equipment damage and product spoilage. Inefficient purification can lead to unnecessarily high operating and maintenance costs.
With over 40 years of compressed air purification experience behind us, Next has developed an extensive line of air / gas filtration products with a range of efficiencies and optional features to cost effectively meet any of your needs. Our pre-filters and post-filters can be configured to suit the requirements of your specific application.

- Dust Particles (from Ambient air and/or desiccant)
- Liquid Water and Moisture Vapor
- Liquid Oil and Oil Vapor
- Hydrocarbon Vapor
- Rust Particles
- Pipe Scale
- Acidic condensates