EHD Series (200-3,500 CFM)
Heated Regenerative Dryers
Next’s Externally Heated twin tower Desiccant Dryers are engineered for exceptional performance and durability to work under harsh conditions in any environment. The EHD Series dryer incorporates global standards by rating our pressure vessels at (200 PSIG 125-1600 CFM & 150 PSIG 2000 CFM & UP) including ASME, and CRN Certifications with added UL, CUL, electrical certification.
Next’s comprehensive option adders for the EHD series dryers allow the dryer to meet any application it is dealt with. The EHD twin tower desiccant compressed air dryers are designed to remove water vapor from your compressed air lowering the pressure dewpoint to -40°F/-40°C.
Designed for the most demanding environments, low pressure drops, and consistent dew point performance are key benefits of the dryer range. As the size of your compressed air system increases, it becomes more important to reduce purge air consumption. The EHD range does just that with the purge rate averaging 7% conserving compressed air and saving you money.
The Next EHD series dryers utilize process air for regeneration of the desiccant bed like the heatless designs. However, this expanded process air is heated prior to entering the of-line bed, significantly reducing the required consumed during depressurization of the offline desiccant tower.
EHD Series Features
- UL, CUL, electrical certifications
- ASME, CRN Code Welded Pressure Vessel certification
- Stainless Steel Angle Body Valves / Butterfly valves
- Optimal tower size for low velocities, high contact time and minimal desiccant fluidization
- Tower Pressure relief Valves
- Purge adjustment valve to control purge flow
- Purge Flow indicator indicates rate
- Horizontal Purge Exhaust mufflers for quiet operation
- Tower Pressure Gauges
- Stainless steel desiccant strainers, supports air diffusers to prevent channeling.
- Counter-current re-pressurization
- NEMA-12 electrical enclosure
- Field adjustable dew point
- Separate drain and fill port
- Separate safety pressure relief valve for each tank
- Tower pressure gauges
- Fail-safe design in case of power failure
- Common alarm contact
NHDC-S7 Controller
- 7” Color touch screen HMI interface
- Energy management system
- Main display shows the following information
- Dewpoint
- Drying, Regenerating, and Repressurizing Side
- Time Remaining for each state
- Outputs 10+
- Digital Dewpoint Trend
- Alarm status
- Alarm log
- Process History
- Energy Savings
- Filter maintenance indicator
- Modbus TCP communication
- Remote Start Stop
Standard operating Voltage
- 460V / 3 PH / 60 HZ – Standard
- 575V / 3 PH / 60 HZ – Optional+
- 400-380V / 3 PH / 50 HZ – Optional+
Pre & Post Filtration (Optional+)
- Post-filtration grade μm 1.0
- Pre-filtration grade μm 0.01
Pressure Vessel Certification
- ASME, CRN (BPD-125-2,500) All Provinces
- Desiccant fill and drain ports
- 1/16” corrosion allowance
- Operating pressure gauge on each vessel
- Pressure relief Valve on each vessel
Min/Max inlet air temperature
- 38/120 ° F
- 3/ 48 ° C
Design Pressure:
- 200 psig
- 13.7 bar
Min/ Max Operating Pressure:
- 80 / 150 Psig
- 5.5/10.3 Bar
Control Panel Certification
- UL, CUL,
- CSA- Optional+
Average Purge Air
- 7%
Standard outlet pressure Dew Point
- -40° F / C
Controller
- 7” Siemens HMI Touch Screen Controller
- 7” Allen Bradley Touch Screen Controller – (Optional+)
Model EHD Series Dryers
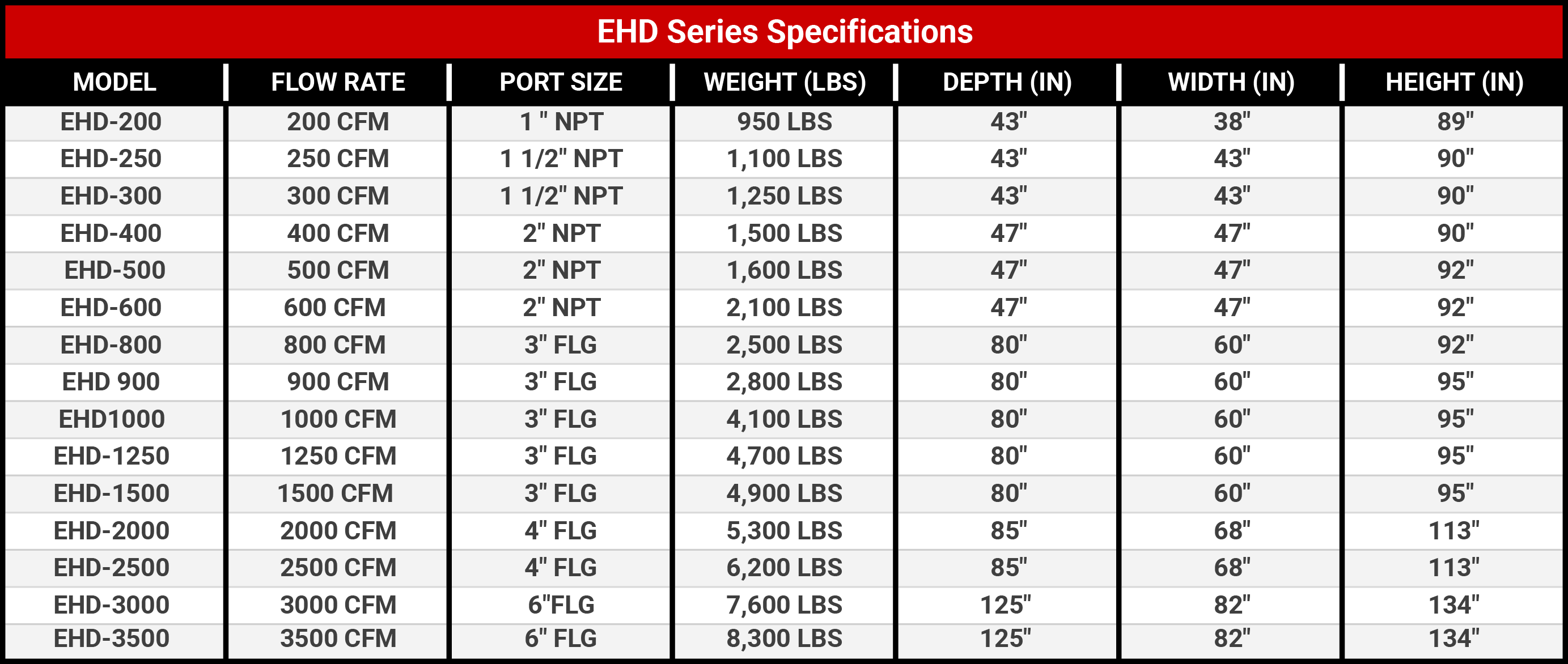
*Additional Flows Available Upon Request
Correction Factors


Air flow capacity = Operating Pressure x Inlet air Temperature
Correction Sample:
If a compressor delivers 500 scfm at 120 psi pressure with a 120°F inlet temperature, please choose your dryer model as follows:
(500 scfm / 1.08 / .75) =617 scfm, therefore an EHD-600 would be needed
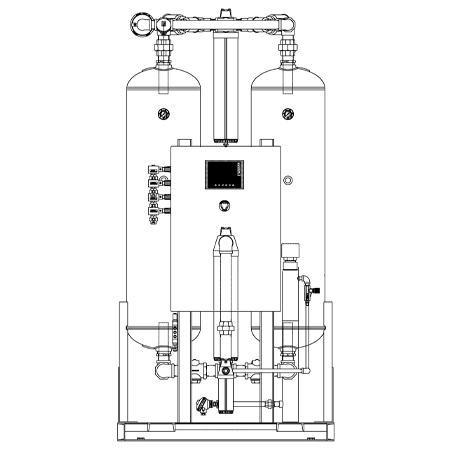
EHD Optional Features
ALTERNATE VOLTAGES+
- ALT-V-5: 575 VOLTS / 3 PHASE / 60 HZ
- ALT-V-6: 400-380 VOLTS / 3 PHASE / 50 HZ
CONSTRUCTION
- TAG: STANDARD STAINLESS STEEL ID TAG
- NYM: NO YELLOW METAL
- SP-DIM: SPECIAL – DIMENSION
- SP-FLT: SPECIAL FILTER CONFIGURATION
- CSA: CANADIAN STANDARDS ASSOCIATION
- CRN: CANADIAN REGISTRATION NUMBER (3000+ CFM)
- BTS: BUILT TO SUITE
- IOPG: INLET-OUTLET PRESSURE GAUGE
- IOTG: INLET-OUTLET TEMPERATURE GAUGE
- TTG: TANK MOUNTED TEMPERATURE GAUGE
- VMI: VISUAL MOISTURE INDICATOR
- SST: STAINLESS STEEL CONTROL AIR TUBING
- CR: CONTROL LINE PRESSURE REGULATOR
- EPH: ELECTRICAL PANEL HEATER
- AC: AFTER COOLER
ELECTRICAL ENCLOSURE+
- N4: NEMA 4 ELECTRICAL ENCLOSURE
- N4X: NEMA 4X STAINLESS STEEL
- N7: NEMA 7 EXPLOSION PROOF
CONDENSATE DRAIN+
- FD: CONDENSATE FLOAT DRAIN
- EZLD: ELECTRONIC ZERO LOSS DRAIN
- MZLD: MECHANICAL ZERO LOSS DRAIN
- HPTD: HIGH PRESSURE TIMER DRAIn
PACKAGES +
- LAP: LOW AMBIENT PACKAGE
- SZ: SUBZERO PACKAGE
- RS: RENTAL SKID
- ZP: ZERO PURGE
DEWPOINT & DIGITAL MONITORING+
- DCC+DDP: DEMAND CYCLE CONTROL
- DDPM -40: DIGITAL DEW POINT MONITOR (-40° F/C)
- DCA: DRY CONTACT ALARM
- ESS: EMERGENCY STOP SWITCH
- RSS: REMOTE START / STOP
BYPASS +
- 3VBP: THREE VALVE BY-PASS
- 9VBP: NINE VALVE BY-PASS
CONTROLLERS+
- ALT-C-3: NBPABC (ALLEN BRADLEY INTERFACE)
- ALT-C-5: NBPI (IDEC INTERFACE)
FILTRATION +
- MF: MOUNTED FILTRATION
- SP-F: SPECIAL FILTER CONFIGURATION
- FS: FILTER SKID (ISLAND)
Your next step toward working with NEXT Air & Gas is to contact us for a Quote. Fill out the information below and give us the appropriate information needed to get started. Be sure to fill out all the contact information and our team will reach out with any questions or concerns.
If you’d rather speak to Sales Engineering, feel free to contact us at (865) 635-8178.
Below are links to product information and brochures. Please click and download at your convenience. If you have any questions or suggestions on materials you think would be helpful, please call us at (865) 635-8178.
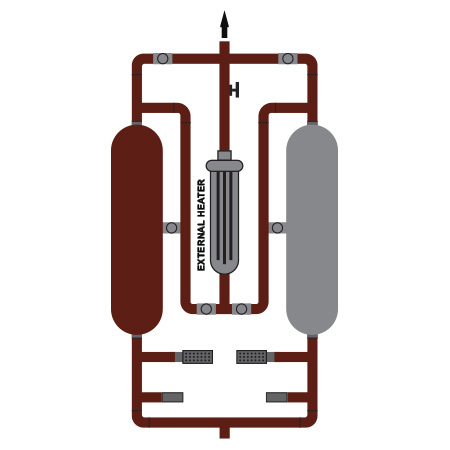
Principle of Operation
The Next EHD series is equipped with an external electric heater to raise the temperature of purge air. The higher the temperature, the greater the capacity of air to absorb moisture, thus heating of the pure air reduces the volume of dry air required for regeneration. Purge air is heated by an industrial quality, low watt density long life electric heater. The heater is in a tube through which purge air flows in an unrestricted manner. Use of the heater tube through which purge air flows in an unrestricted manner. Use of the heater tube assures uniform heat distribution. The heater element does not meet the desiccant, thereby the heater prevents physical deterioration of the desiccant material.
EHD dryers use an additional heat source-reducing process air loss during the regeneration process. The additional heat source helps enhance the drying and regeneration process while saving energy.
Overview
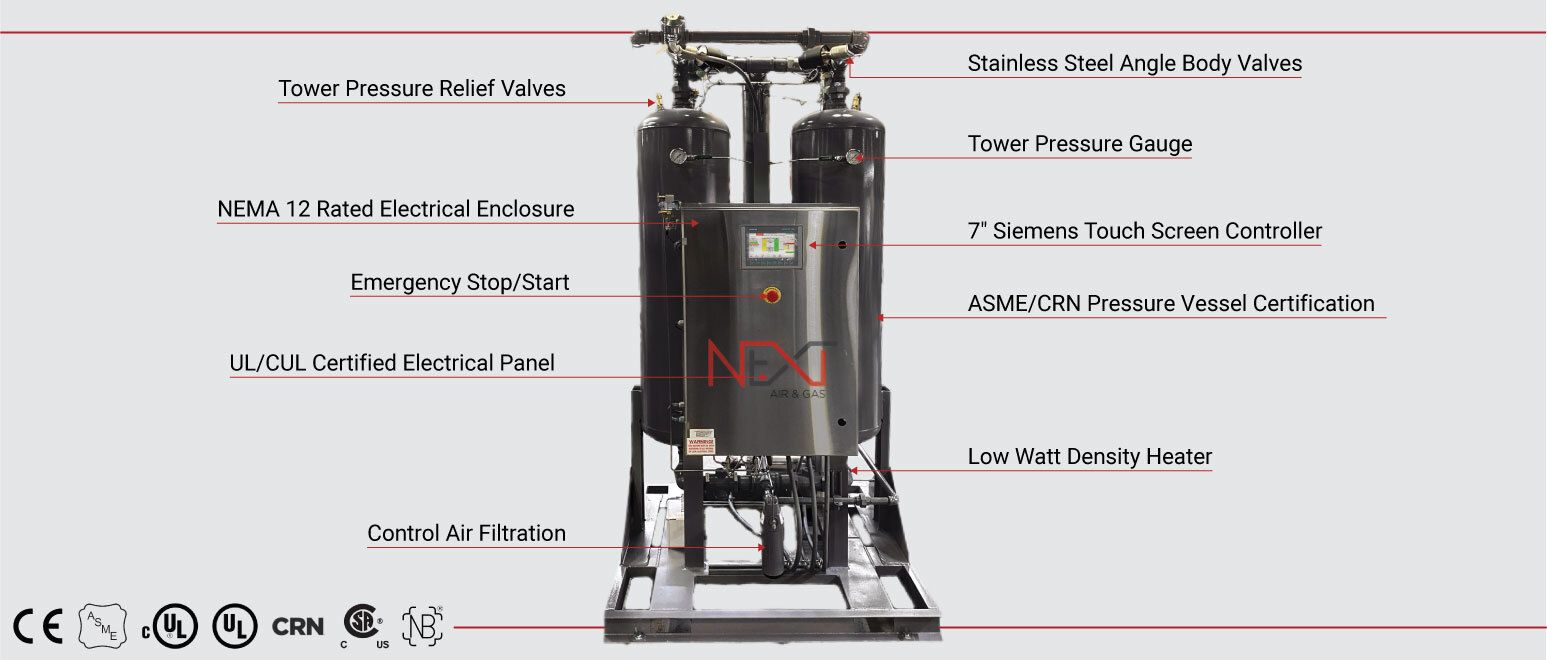
Next Air & Gas Performance Advantages
The performance of any desiccant dryer depends on the quality of its key components. Next Air & Gas uses the best available valves, controllers and desiccant. With accurately designed and sized components, the dryers are manufactured to provide you with years of trouble-free operation.
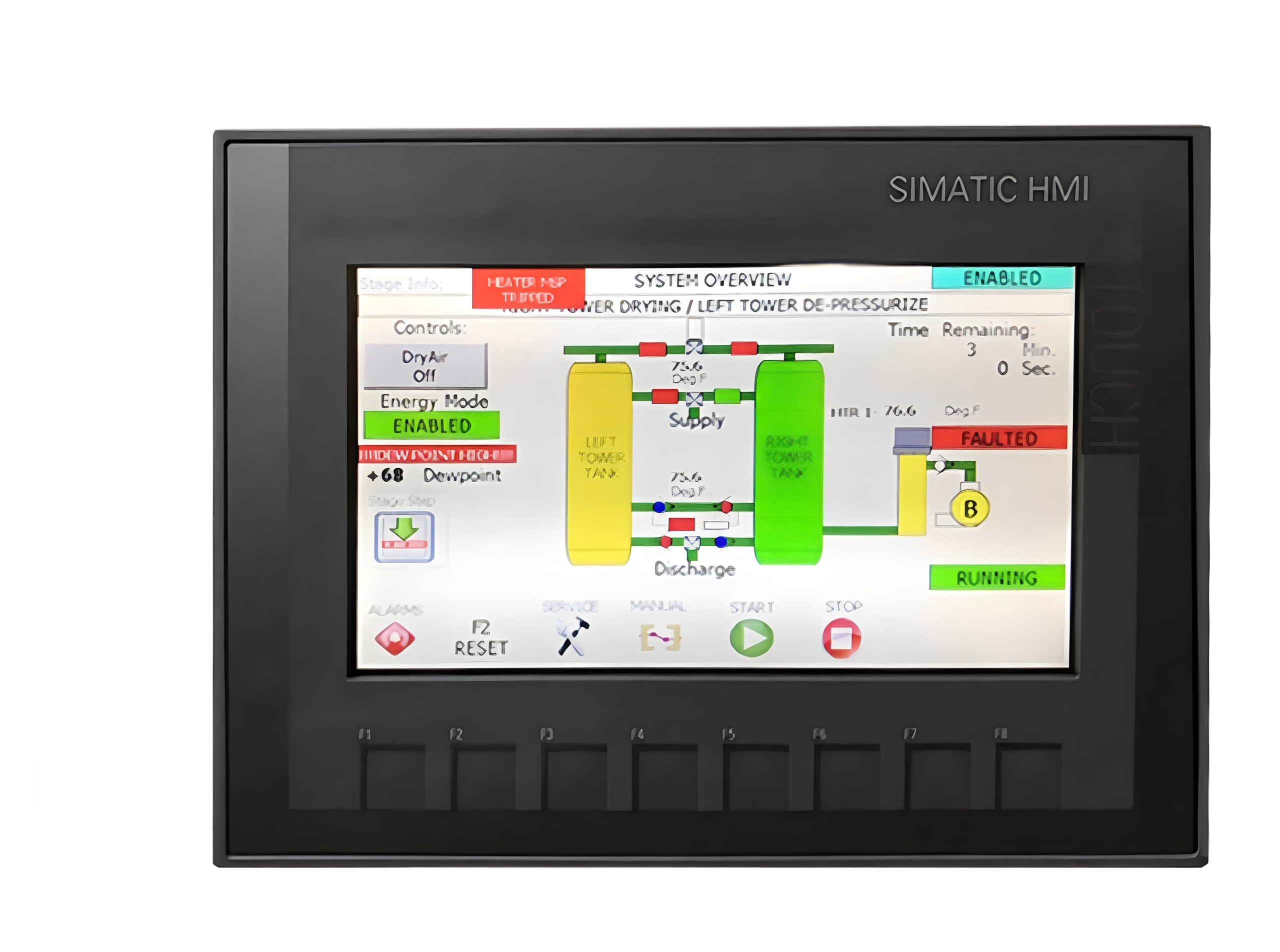
HMI Touchscreen Interface
The entire drying/ regeneration cycle is controlled by a Siemens Micro-Logix programmable logic controller (PLC), among the most reliable controllers available. The plc is supplied with a 7″ Siemens touch screen HMI display which, among other items, will provide the operator with the following information.
- Indicate alarm when a system fault is detected and identify the specific fault
- Indicate status of each vessel (drying, regenerating, or in standby)
- Indicated time remaining of each phase of the cycle

Digital Dewpoint Transmitters Optimize Operations
NEXT’s FAN-500 and 510 are the ideal dew point sensors for monitoring dew point changes for our desiccant dryers. If your needs include a set dew point of -40° F or -100° F, NEXT’s range of dew point sensors has it covered.
- Modbus-RTU Interface
- Higher Resolution of Sensor Signal Through Improved Evaluation Electronics
- Integrated Display (Fan-500)
- Pressure-tight up to 5,000 psig./350 Bar (special version)
- Extreme Long-Term Stability
- Quick Response Time
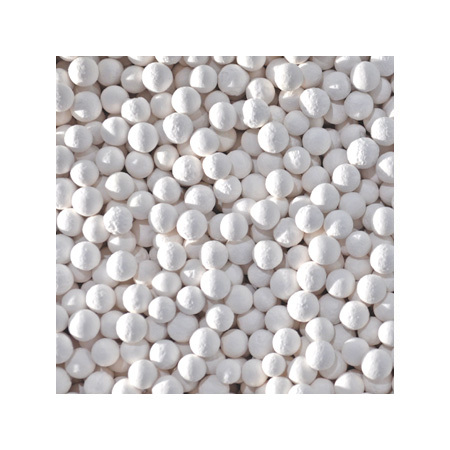
Quality Desiccant Media
Next Air & Gas uses a mixture of adsorption media in its heatless range of desiccant dryers to achieve consistent dewpoint. Activated Alumina, Molecular Sieve and Silica Gel are used in varying ratios depending on the application. The long lasting, high crush strength media has a very high surface/volume ratio. Beaded activated alumina is used as the adsorption media in heated desiccant dryers. The beads exhibit a very high internal surface area and high moisture separation efficiency. Each lot of desiccants is thoroughly tested for density, moisture content, abrasion resistance, surface area, mesh size and granule strength to assure that it meets strict design requirements.
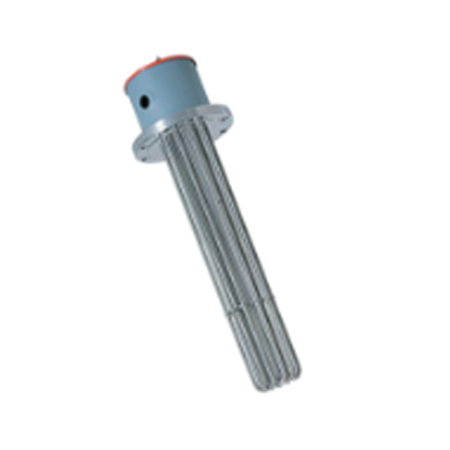
Low Watt Density Heaters
Ambient air from the centrifugal blower is directed through an electric resistance heater to elevate the temperature to 400F for regeneration of the off-stream bed. Heaters are designed with a low watt density for low surface temperatures and long element life. The heating elements are contained within tubes with are themselves protected with direct contact type ” K thermocouples
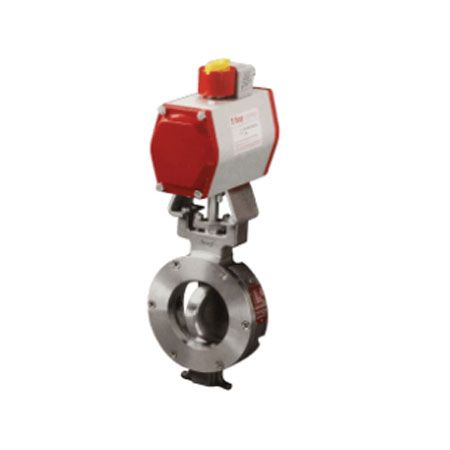
Butterfly Valves for Precise Control
These versatile, high-performance butterfly valves are used by Next Air & Gas to provide you with precision control and complete bubble-tight shut off. The digitally controlled actuators provide an easy PLC interface and feature fast response time. The tongue-and-groove seat design feature ensures complete isolation of flowing media from the body and stem. Rugged and reliable, these valves are designed to provide years of trouble-free service.
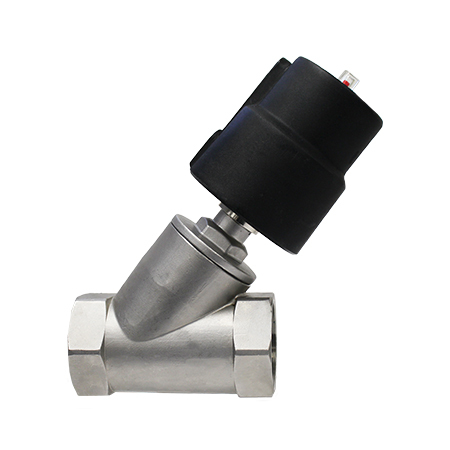
Angle Body Piston Valve
These high-performance, 2-way direct acting valves are designed for reliability and durability. They utilize a profiled disc in conjunction with a high-resolution compact positioner and linear feedback potentiometer to provide precise proportional flow. The stainless-steel internals and a tough fiber composite actuator body, along with the use of oversized bearing and Viton® seals, make it possible to consistently provide smooth piston movement for years of trouble-free service. Angle body valves are used to control depressurization of the regenerating vessel and to control the dry purge air flow during the cooling phase of the process. Angle body valves offer high flow rates and long service life in compact, economical packages.
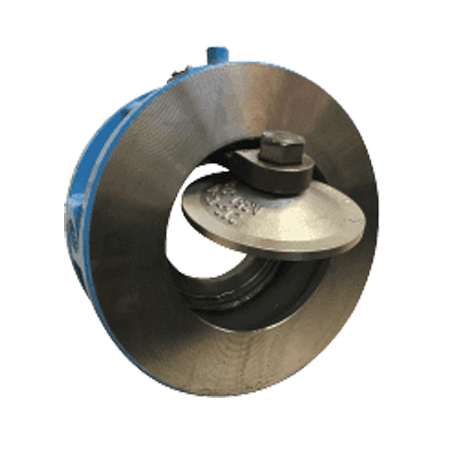
State-of-the-art Check Valve
Check valves are used at the dryer outlet and on the hot air regeneration lines. They are designed with large ports to minimize pressure loss. Outlet check valves incorporate a stainless-steel disc and O-rings while hot air regeneration valves utilize a metal-to-metal seal to withstand elevated temperatures. High Temperature, wafer-combination swing check valves are flow activated. The elliptical shape of the inlet port accelerates the inlet media through the valve. The disc’s angle and shape allow the air to travel faster around the disc, thus creating lift like an aircraft wing, and opens the valve in the full position even at a low flow rate
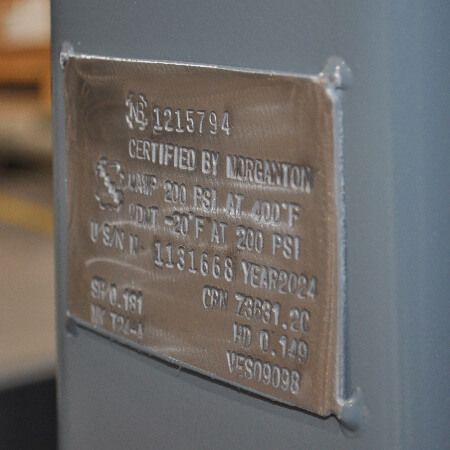
PRESSURE VESSELS
EHD desiccant vessels have been designed with a wide diameter for a large cross- sectional flow area. This results in a low flow velocity which minimizes both pressures drop across the bed and attrition of the desiccant itself. The Vessels incorporate the flowing additional features:
- Stainless steel inlet and outlet air diffusers for even flow distribution
- Stainless steel bed support on units above 3,000 scfm
- Desiccant fill and drain ports
- 1/16” corrosion allowance
- Operating pressure gauge on each vessel
- Pressure relief Valve on each vessel
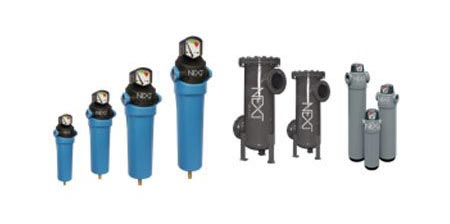
PREMIUM PLEATED & WRAPPED COMPRESSED AIR FILTERS
Next offers superior filtration from 1 micron to 0.01 micron, and connections from ½” NPT to 10” FLG. Next Filters are engineered to be efficient under any parameter. Next elements offer a durable element construction with an efficient drain layer to ensure continued performance after optimal element change periods.